In a show of force against Pyongyang, South Korea and the United States conducted a round
of combined ballistic missile drills on Saturday, within six hours of North Korea's missile
launch.
Seoul's Joint Chiefs of Staff announced that at 5:45 A.M. local time, they fired a volley
of Korean Hyunmoo-2 missiles and American ATACMSs into the East Sea.
They said the live-fire exercise demonstrated their capabilities for a "precise strike on
the enemy's leadership"...while the U.S. military also stressed the "deep-strike precision capabilities"
of the ATACMSs as well as their rapid deployment.
The Joint Chiefs also said that this demonstrates the South Korea-U.S. alliance will not tolerate
any provocations by Pyongyang.
For more infomation >> S. Korea, U.S. carry out joint ballistic missile drills within hours of N. Korea launch - Duration: 0:48.-------------------------------------------
S. Korea to expand defense capabilities, U.S. flies B-1B bombers over peninsula - Duration: 1:34.
Amid North Korea's continuing missile provocations,...
South Korea is planning to expand its defense capabilities.
On Sunday, Defense Minister Song Young-moo said Seoul will upgrade its Patriot missile
system to better protect the nation's capital area.
Song inspected a Patriot missile site... where he reaffirmed that Seoul will soon establish
its own anti-missile system.
Meanwhile on Sunday, South Korea continued its joint military drills with the U.S.
Two U.S. B-1B bombers flew over the Korean peninsula in the morning, joined by four South
Korean fighter jets.
Seoul and Washington had kicked off a round of air force exercises within about six hours
of the regime's ICBM launch late Friday evening.
The B-1B Lancer is known as the backbone of Washington's long-range bomber force.
It's a multi-mission weapon system that can reach the Korean Peninsula in just a couple
of hours from its base in Guam.
In a statement, the U.S. 7th Air Force said the training was to demonstrate America's
"ironclad" commitment to its allies.
Washington is also reportedly planning to test-launch its missile defense system THAAD
-- a unit stationed in Alaska -- possibly as soon as this weekend.
Lee Unshin Arirang News.
-------------------------------------------
S. Korea, U.S. carry out joint ballistic missile drills within hours of N. Korea launch - Duration: 0:46.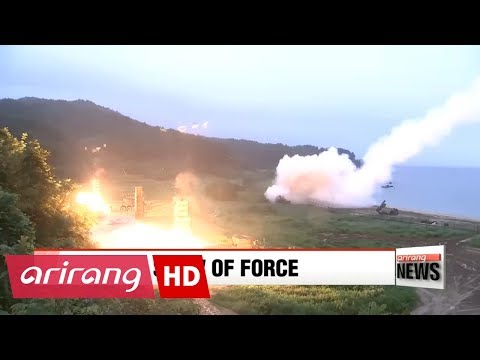
In a show of force against Pyongyang, South Korea and the United States swiftly conducted
a round of combined ballistic missile drills on Saturday that came within six hours of
North Korea's missile launch.
Seoul's Joint Chiefs of Staff announced that at 5:45 A.M. local time, they fired a volley
of Korean Hyunmoo-2 missiles and American ATACMSs into the East Sea.
They said the live-fire exercise demonstrated their capabilities for a "precise strike on
the enemy's leadership"...while the U.S. military also stressed the "deep-strike precision capabilities"
of the ATACMSs as well as their rapid deployment.
The Joint Chiefs of Staff also said this demonstrates the South Korea-U.S. alliance will not tolerate
any provocations by Pyongyang.
-------------------------------------------
S. Korea, U.S., Japan to cooperate to deter future threats from North Korea - Duration: 1:42.
We begin with the big video conference last night between the top security officials of
South Korea, the United States and Japan.
Top of the agenda was how to deal with North Korea,... and the three nations reaffirmed
that their ultimate goal is to bring the rogue state back to the table for talks.
Our Blue House correspondent Hwang Hojun leads us off.
Less than a week after North Korea thumbed its nose at the international community with
a highly provocative ICBM test,... the top security officials of South Korea, the United
States and Japan held their first three-way video conference call on deterring further
threats from the Kim Jong-un regime.
During the 70-minute-long meeting that began at 9 pm Thursday, Korea time, Seoul's National
Security Office Chief Chung Eui-yong and his American and Japanese counterparts, H.R. McMaster
and Shotaro Yachi-- agreed that Pyongyang's ICBM launch posed a grave threat to peace...
and the stability of the Korean Peninsula, Northeast Asia and the wider international
community.
North Korea fired off two ICBMs in July alone.
According to South Korea's presidential office, all three vowed to continue consistently applying
maximum pressure on the regime, including through UN Security Council resolutions.
But the security chiefs, again, stressed that dialogue with the North is possible under
the right conditions, but sanctions and pressure are necessary for that to happen.
Chung Eui-yong, in particular, reiterated the ultimate goal is to bring North Korea
back to the table for talks, and they must be careful not to stir up tensions on the
Korean Peninsula unnecessarily.
Hwang Hojun, Arirang News.
-------------------------------------------
S. Korea's FM, U.S. Secretary of State discuss North Korea-related issues - Duration: 0:46.
We begin this morning from on the diplomatic front...
South Korea's Foreign Minister Kang Kyung-wha and U.S. Secretary of State Rex Tillerson
have exchanged their views on a new UN Security Council resolution,... in response to North
Korea's recent ballistic missile launch.
Speaking on the phone for around half-an-hour on Thursday evening,... officials said Kang
and Tillerson were on the same page on responding strongly to further North Korean provocations.
The top diplomats also assessed the current security situation on the Korean Peninsula...
and followed-up on the results of last month's summit between Presidents Moon Jae-in and
Donald Trump.
The phone conversation was the first since North Korea launched what it claimed to be
an ICBM on July 4th.
-------------------------------------------
First submarine export as S. Korea hands over vessel to Indonesia - Duration: 2:02.
South Korea is set to become a part of an exclusive club: Nations that export submarines.
Quite a rapid transition considering Seoul first received the technology to build such
vessels just 3 decades ago.
Cho Sungmin dissect the significance of this maiden event.
A Korean-built submarine rolls out to sea.
Next stop: Indonesia.
This submarine,named 'Nagapasa' , is ready for a handover to Indonesia's Ministry of
Defense at a shipyard in Geoje , a city in Gyeongsangnam-do province.
Nagapasa can travel for 19-thousand-kilometers, a round trip between Korea and Los Angeles,
without making any stop at a port, and is also equipped with eight offensive torpedo
tubes, along with other cutting-edge weaponry.
Indonesian Defense Minister, Ryamizard Ryacudu said he is pleased with the submarine.
"I am expecting that this 1,400-ton submarine will act as a key strategic weapon for our
maritime security in Indonesia."
As Daewoo Shipbuilding & Engineering delivers this submarine to Indonesia, it marks the
first submarine export by a Korean company.
Daewoo took on a one-point-one-billion U.S. dollar contract in 2011 to provide Indonesia
with three submarines, the other two of which are currently under construction.
"We believe that we can guarantee the cost of the technology we have invested in.
We hope our technology can contribute to the Korean navy as well as continuing our partnership
with the Indonesian navy."
The handover of the vessel is regarded as a Korean success in commercializing the technology
which the country first received from Germany in 1988.
In the space of just 30 years, Korea has developed its submarine industry to the extent that
it is now a submarine exporting nation.
With the sale of these three vessels, Korea, joins an elite group of submarine exporting
countries, including the U.K., France, Russia and Germany.
Won Jung-hwan, Arirang News.
-------------------------------------------
S. Korea's FM, U.S. Secretary of State reaffirm cooperation on N. Korea's nukes and missiles - Duration: 2:16.
The top diplomats of Seoul and Washington reaffirmed cooperation in dealing with North
Korea's nuclear and missile programs.
The talks come as U.S. defense officials expressed concerns Pyongyang will be able to field a
nuclear-tipped ICBM soon.
Connie Kim shares with us what was discussed.
South Korea's Foreign Minister Kang Kyung-wha and U.S. Secretary of State Rex Tillerson
have exchanged views on a new UN Security Council resolution in response to North Korea's
recent ballistic missile launch.
Speaking on the phone for around half-an-hour on Thursday evening, they agreed on ways to
prevent further North Korean provocations... and pressure the regime to abandon its nuclear
weapons.
"The leaders agreed to continue our close coordination in response to North Korea's
destabilizing violations of UN Security Council resolutions and hold North Korea accountable
for its unlawful actions."
Kang and Tillerson also assessed the current security situation on the Korean Peninsula...
and followed-up on the results of last month's summit between Presidents Moon Jae-in and
Donald Trump.
Close cooperation between the allies is as important as ever,... especially considering
that the Pentagon's Defense Intelligence Agency said this week that North Korea would be able
to field a nuclear-capable ICBM next year.
Responding to that report,… a senior U.S. official, who asked not to be named, said
the North is at a point of attaining a nuclear-tipped ballistic missile "pretty soon."
This is in line with U.S. Army chief Mark Milley's remarks that North Korea's ICBM threat
is advancing faster than most people thought possible.
"North Korea has advanced significantly quicker than many of the expected.
Their intercontinental ballistic missile capability could possibly strike the United States.
More to follow but the time has shortened significantly."
While there are also analysts who do not hold the same assessment as the Pentagon,... it's
hard to argue that North Korea isn't making big strides forward in its missile development.
CIA has already labeled Pyongyang as a massive liability risk and said its mission center
on North Korea is reviewing various options on the regime... when diplomacy does not work
any longer.
Connie Kim, Arirang News.
-------------------------------------------
S. Korea, U.S. in joint missile drills, Washington to test THAAD in Alaska - Duration: 0:48.
Following Pyongyang's missile launch ,... South Korea and the United States carried out a
round of combined ballistic missile drills.
The live-fire exercises kicked off on Saturday on Korea's east coast... in a demonstration
to Pyongyang of the two allies' firepower.
The drills involved South Korea's road-mobile ballistic missile, the Hyunmoo -2, and the
U.S. forces' Army Tactical Missile System.
Officials say the drills showed the allies' ability to carry out "precise strikes on the
enemy's leadership."
Washington is planning to test-launch its missile defense system THAAD -- a unit stationed
in Alaska.
According to the A-P, the launch is scheduled to start as early as Saturday night local
time.
-------------------------------------------
S. Korea, U.S., Japan to cooperate to deter future threats from North Korea - Duration: 1:45.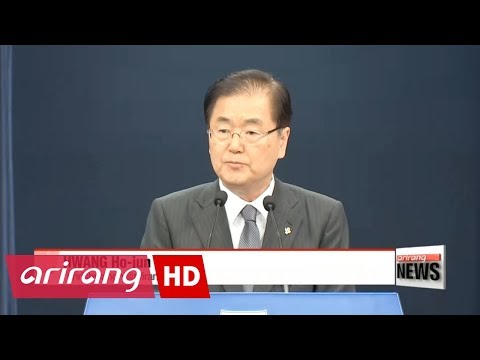
We begin with the big video conference last night between the top security officials of
South Korea, the United States and Japan.
Top of the agenda was how to deal with North Korea,... and the three nations reaffirmed
that their ultimate goal is to bring the rogue state back to the table for talks.
Our Blue House correspondent Hwang Hojun starts us off.
Less than a week after North Korea thumbed its nose at the international community with
a highly provocative ICBM test,... the top security officials of South Korea, the United
States and Japan held their first three-way video conference call on deterring further
threats from the Kim Jong-un regime.
During the 70-minute-long meeting that began at 9 pm Thursday, Korea time, Seoul's National
Security Office Chief Chung Eui-yong and his American and Japanese counterparts, H.R. McMaster
and Shotaro Yachi-- agreed that Pyongyang's ICBM launch posed a grave threat to peace...
and the stability of the Korean Peninsula, Northeast Asia and the wider international
community.
North Korea fired off two ICBMs in July alone.
And the top security advisors reached an understanding that they won't sit back and watch them continue.
"The three parties agreed to maximize pressure on North Korea, including through UN Security
Council resolutions, to prevent future provocations."
But the security chiefs, again, stressed that dialogue with the North is possible under
the right conditions, but sanctions and pressure are necessary for that to happen.
Chung Eui-yong, in particular, reiterated the ultimate goal is to bring North Korea
back to the table for talks, and they must be careful not to stir up tensions on the
Korean Peninsula unnecessarily.
Hwang Hojun, Arirang News.
-------------------------------------------
S. Korea's FM, U.S. Secretary of State reaffirm cooperation on N. Korea's nukes and missiles - Duration: 2:18.
South Korea and the United States have reaffirmed their cooperation on North Korea's nuclear
and missile programs.
The talks come as U.S. defense officials have expressed concern Pyongyang will be able to
field a nuclear-tipped ICBM within the next twelve to 18 months.
Connie Kim has more.
South Korea's Foreign Minister Kang Kyung-wha and U.S. Secretary of State Rex Tillerson
have exchanged views on a new UN Security Council resolution in response to North Korea's
recent ballistic missile launch.
Speaking on the phone for around half-an-hour on Thursday evening, they agreed on ways to
prevent further North Korean provocations... and pressure the regime to abandon its nuclear
weapons.
"The leaders agreed to continue our close coordination in response to North Korea's
destabilizing violations of UN Security Council resolutions and hold North Korea accountable
for its unlawful actions."
Kang and Tillerson also assessed the current security situation on the Korean Peninsula...
and followed-up on the results of last month's summit between Presidents Moon Jae-in and
Donald Trump.
Close cooperation between the allies is as important as ever,... especially considering
that the Pentagon's Defense Intelligence Agency said this week that North Korea would be able
to field a nuclear-capable ICBM next year.
Responding to that report,… a senior U.S. official, who asked not to be named, said
the North is at a point of attaining a nuclear-tipped ballistic missile "pretty soon."
This is in line with U.S. Army chief Mark Milley's remarks that North Korea's ICBM threat
is advancing faster than most people thought possible.
"North Korea has advanced significantly quicker than many of the expected.
Their intercontinental ballistic missile capability could possibly strike the United States.
More to follow but the time has shortened significantly."
While there are also analysts who do not hold the same assessment as the Pentagon,... it's
hard to argue that North Korea isn't making big strides forward in its missile development.
CIA has already labeled Pyongyang as a massive liability risk and said its mission center
on North Korea is reviewing various options on the regime... when diplomacy does not work
any longer.
Connie Kim, Arirang News.
-------------------------------------------
S. Korea, U.S., Japan to cooperate to deter future threats from N. Korea - Duration: 0:42.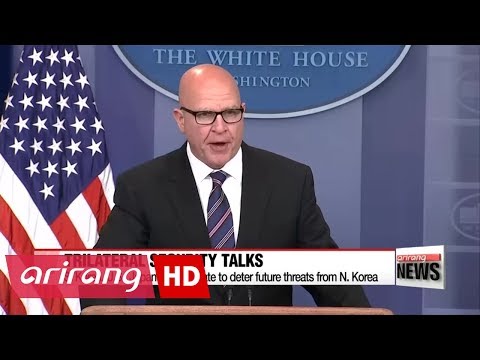
The top security officials of South Korea, the United States and Japan held their first
three-way video conference late last night on North Korea's continual nuclear and missile
provocations.
South Korea's presidential office says Seoul's National Security Office Chief Chung Eui-yong
and his American and Japanese counterparts, H.R. McMaster and Shotaro Yachi-- agreed that
Pyongyang's latest ICBM launch posed a grave threat to peace and the stability of the international
community.
All three vowed to continue applying maximum pressure on the regime.
But the security chiefs, again, acknowledged that the ultimate goal is to bring North Korea
back to the table for talks.
-------------------------------------------
S. Korea's FM, U.S. Secretary of State reaffirm cooperation on N. Korea's nukes and missiles - Duration: 2:18.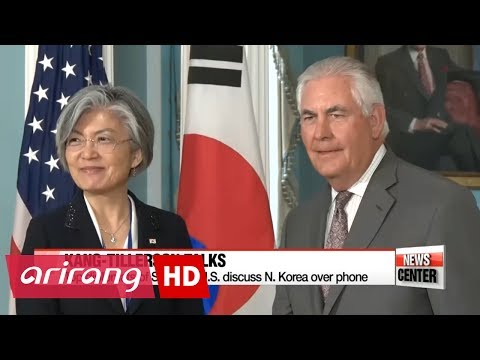
The top diplomats of Seoul and Washington reaffirmed cooperation in dealing with North
Korea's nuclear and missile programs.
The talks come as U.S. defense officials expressed concerns Pyongyang will be able to field a
nuclear-tipped ICBM within the next twelve to 18 months.
Connie Kim shares with us what was discussed.
South Korea's Foreign Minister Kang Kyung-wha and U.S. Secretary of State Rex Tillerson
have exchanged views on a new UN Security Council resolution in response to North Korea's
recent ballistic missile launch.
Speaking on the phone for around half-an-hour on Thursday evening, they agreed on ways to
prevent further North Korean provocations... and pressure the regime to abandon its nuclear
weapons.
"The leaders agreed to continue our close coordination in response to North Korea's
destabilizing violations of UN Security Council resolutions and hold North Korea accountable
for its unlawful actions."
Kang and Tillerson also assessed the current security situation on the Korean Peninsula...
and followed-up on the results of last month's summit between Presidents Moon Jae-in and
Donald Trump.
Close cooperation between the allies is as important as ever,... especially considering
that the Pentagon's Defense Intelligence Agency said this week that North Korea would be able
to field a nuclear-capable ICBM next year.
Responding to that report,… a senior U.S. official, who asked not to be named, said
the North is at a point of attaining a nuclear-tipped ballistic missile "pretty soon."
This is in line with U.S. Army chief Mark Milley's remarks that North Korea's ICBM threat
is advancing faster than most people thought possible.
"North Korea has advanced significantly quicker than many of the expected.
Their intercontinental ballistic missile capability could possibly strike the United States.
More to follow but the time has shortened significantly."
While there are also analysts who do not hold the same assessment as the Pentagon,... it's
hard to argue that North Korea isn't making big strides forward in its missile development.
CIA has already labeled Pyongyang as a massive liability risk and said its mission center
on North Korea is reviewing various options on the regime... when diplomacy does not work
any longer.
Connie Kim, Arirang News.
-------------------------------------------
Seoul will push for strong UN sanctions on N. Korea: S. Korea's FM - Duration: 0:47.
South Korea will be pushing for strong UN Security Council sanctions on the heels of
North Korea's second long-range ballistic missile launch in less than a month.
Foreign Minister Kang Kyung-wha, holding an emergency meeting with senior ministry officials,...
directed them to pour their efforts into arranging a swift UN Security Council meeting and bringing
out strong response measures from the United Nations.
Kang said she will use the upcoming ASEAN Regional Forum, the only multilateral conference
North Korea takes part in,.. to discuss ways to prevent provocations and send strong warnings
on Pyongyang.
It has been confirmed North Korea will be attending,... with attention set on whether
Kang will hold a one-on-one with North Korean foreign minister Ri Yong-ho .
-------------------------------------------
S. Korea and U.S. resume discussions on deployment of additional THAAD launchers - Duration: 1:35.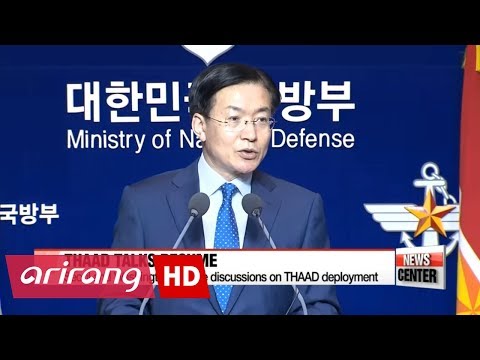
Following North Korea's latest provocation, Seoul and Washington look into completing
the stationing of THAAD in the peninsula.
This response came quickly, as the regime test-fired an ICBM capable of reaching the
U.S. west coast.
Kim Hyun-bin has our top story.
Seoul and Washington have resumed discussions to swiftly deploy the U.S. advanced missile
defense system THAAD to Seongju County,... some 300 kilometers southeast of the capital.
Defense ministry spokesperson Moon Sang-gyun says the two countries will first decide when
and how the deployment will take place.
"We will discuss the deployment of the remaining launcher with the U.S.
Once the talks are complete we will install the launchers."
. .
Following Pyongyang's test-firing of an ICBM last Friday, President Moon ordered the military
to resume the deployment of THAAD, reversing his previous decision to suspend the deployment...
until an environmental assessment is carried out.
A THAAD battery consists of six launchers, but only two launchers are currently operational
in Seongju.
President Moon said the other four will be deployed... following discussions between
the allies, though the timing is still undecided.
The decision by South Korea and the U.S. to deploy THAAD was made last year amid the regime's
continuous testing and enhancing of its nuclear and missile capabilities.
Military experts say that the latest ICBM could reach the west coast of the United States.
Meanwhile, the South Korean military is closely monitoring the North for a possible nuclear
test, which it believes could happen this year.
Kim Hyun-bin, Arirang News.
-------------------------------------------
S. Korea and U.S. resume discussions on deployment of additional THAAD launchers - Duration: 1:31.
South Korea and the United States are looking to complete the stationing of the THAAD anti-missile
defense system on the Korean peninsula... this,... following North Korea's latest provocation.
President Moon Jae-in wants to triple the number of THAAD launchers from the current
two to six.
Kim Hyun-bin reports.
Seoul and Washington have resumed discussions to swiftly deploy the U.S. advanced missile
defense system THAAD to Seongju County,... some 300 kilometers southeast of the capital.
Defense ministry spokesperson Moon Sang-gyun says the two countries will first decide when
and how the deployment will take place.
"We will discuss the deployment of the remaining launcher with the U.S.
Once the talks are complete we will install the launchers."
. .
Following Pyongyang's test-firing of an ICBM last Friday, President Moon ordered the military
to resume the deployment of THAAD, reversing his previous decision to suspend the deployment...
until an environmental assessment is carried out.
A THAAD battery consists of six launchers, but only two launchers are currently operational
in Seongju.
President Moon said the other four will be deployed... following discussions between
the allies, though the timing is still undecided.
The decision by South Korea and the U.S. to deploy THAAD was made last year amid the regime's
continuous testing and enhancing of its nuclear and missile capabilities.
Military experts say that the latest ICBM could reach the west coast of the United States.
Kim Hyun-bin, Arirang News.
-------------------------------------------
S. Korea and U.S. resume discussions on deployment of additional THAAD launchers - Duration: 1:34.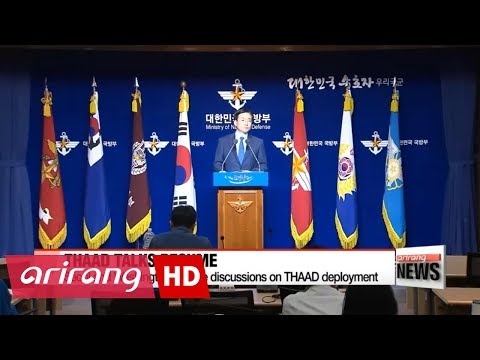
Following North Korea's latest provocation, Seoul and Washington look into completing
the stationing of THAAD in the peninsula.
This response came quickly, as the regime test-fired an ICBM capable of reaching the
U.S. west coast.
Kim Hyun-bin starts us off.
Seoul and Washington have resumed discussions to swiftly deploy the U.S. advanced missile
defense system THAAD to Seongju County,... some 300 kilometers southeast of the capital.
Defense ministry spokesperson Moon Sang-gyun says the two countries will first decide when
and how the deployment will take place.
"We will discuss the deployment of the remaining launcher with the U.S.
Once the talks are complete we will install the launchers."
. .
Following Pyongyang's test-firing of an ICBM last Friday, President Moon ordered the military
to resume the deployment of THAAD, reversing his previous decision to suspend the deployment...
until an environmental assessment is carried out.
A THAAD battery consists of six launchers, but only two launchers are currently operational
in Seongju.
President Moon said the other four will be deployed... following discussions between
the allies, though the timing is still undecided.
The decision by South Korea and the U.S. to deploy THAAD was made last year amid the regime's
continuous testing and enhancing of its nuclear and missile capabilities.
Military experts say that the latest ICBM could reach the west coast of the United States.
Meanwhile, the South Korean military is closely monitoring the North for a possible nuclear
test, which it believes could happen this year.
Kim Hyun-bin, Arirang News.
-------------------------------------------
S. Korea, U.S., Japan to cooperate to deter future threats from North Korea - Duration: 1:39.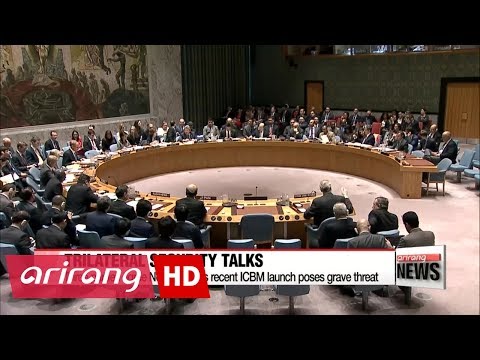
Let's kick off the bulletin with the big video conference last night between the top security
officials of South Korea, the United States and Japan.
Top of the agenda: how to deal with North Korea's continual nuclear and missile provocations.
Hwang Hojun starts us off.
Less than a week after North Korea thumbed its nose at the international community with
a highly provocative ICBM test,... the top security officials of South Korea, the United
States and Japan held their first three-way video conference call on deterring further
threats from the Kim Jong-un regime.
During the 70-minute-long meeting that began at 9 pm Thursday, Korea time, Seoul's National
Security Office Chief Chung Eui-yong and his American and Japanese counterparts, H.R. McMaster
and Shotaro Yachi-- agreed that Pyongyang's ICBM launch posed a grave threat to peace...
and the stability of the Korean Peninsula, Northeast Asia and the wider international
community.
North Korea fired off two ICBMs in July alone.
According to South Korea's presidential office, all three vowed to continue consistently applying
maximum pressure on the regime, including through UN Security Council resolutions.
But the security chiefs, again, stressed that dialogue with the North is possible under
the right conditions, but sanctions and pressure are necessary for that to happen.
Chung Eui-yong, in particular, reiterated the ultimate goal is to bring North Korea
back to the table for talks, and they must be careful not to stir up tensions on the
Korean Peninsula unnecessarily.
Hwang Hojun, Arirang News.
-------------------------------------------
S. Korea's FM, U.S. Secretary of State reaffirm cooperation on N. Korea's nukes and missiles - Duration: 2:05.
South Korea and the United States have reaffirmed their cooperation on North Korea's nuclear
and missile programs.
The talks come as U.S. defense officials have expressed concern Pyongyang will be able to
field a nuclear-tipped ICBM within the next twelve to 18 months.
Connie Kim has more.
South Korea's Foreign Minister Kang Kyung-wha and U.S. Secretary of State Rex Tillerson
have exchanged views on a new UN Security Council resolution in response to North Korea's
recent ballistic missile launch.
Speaking on the phone for around half-an-hour on Thursday evening, they agreed on ways to
prevent further North Korean provocations... and pressure the regime to abandon its nuclear
weapons.
"The leaders agreed to continue our close coordination in response to North Korea's
destabilizing violations of UN Security Council resolutions and hold North Korea accountable
for its unlawful actions."
Kang and Tillerson also assessed the current security situation on the Korean Peninsula...
and followed-up on the results of last month's summit between Presidents Moon Jae-in and
Donald Trump.
Close cooperation between the allies is as important as ever,... especially considering
that the Pentagon's Defense Intelligence Agency said this week that North Korea would be able
to field a nuclear-capable ICBM by next year.
Responding to that report,… a senior U.S. official, who asked not to be named, said
the North is at a point of attaining a nuclear-tipped ballistic missile "pretty soon."
This is in line with U.S. Army chief Mark Milley's remarks that North Korea's ICBM threat
is advancing faster than most people thought possible.
"North Korea has advanced significantly quicker than many of the expected.
Their intercontinental ballistic missile capability could possibly strike the United States.
More to follow but the time has shortened significantly."
While there are also analysts who do not hold the same assessment as the Pentagon,... it's
hard to argue that North Korea isn't making big strides forward in its missile development.
Connie Kim, Arirang News.
-------------------------------------------
Investigation confirms S. Korean spy agency's involvement in presidential election - Duration: 0:52.
An internal probe at South Korea's intelligence agency has revealed that some of its operatives
attempted to influence the outcome of the 20-12 presidential election.
The investigation team announced on Thursday that the National Intelligence Service operated
up to 30 cells aimed at manipulating public opinion in the run-up to the vote.
The spotlight has fallen on Won Sei-hoon , the agency's director from 2009 to 2013,... who
is already on trial for allegedly masterminding a smear campaign,... in favor of then-presidential
candidate Park Geun-hye.
The probe also revealed... that NIS operatives had meddled in the 20-11 and 20-12 parliamentary
elections... while placing opposition candidates under illegal surveillance.
-------------------------------------------
S. Korean defense chief visits USFK combat command - Duration: 0:31.
Seoul's efense minister Song Young-moo... visited the U.S. Army Garrison in Yongsan
for the first time since taking office last month.
Meeting with USFK commander Vincent Brooks, he emphasized the need to retaliate strongly
against North Korea when necessary, while focusing on deterrence.
Song pointed out Pyongyang's recent ICBM launch is a threat not only to South Korea but to
the world.
The minister added the upcoming combined drill, the Ulchi-Freedom Guardian, which starts later
this month, is a good opportunity to display the allies' readiness.
-------------------------------------------
Starve.io Intense fight! - Duration: 2:36.
i need some food :/
oh look some berries :)
i wonder what super hot fire is doing
lets go check
suprise motha f
EY get out my house!
sorry sorry is a prank
superhotfire:now you pay!
nuu plz nuu :'(
TYT to the rescue :D
btw i told TYT to run
POW pow smack pow! wackopow!
i need some fire :/
aaa :)
Wassup bro fight me!!
pow pow smack smack!
decker help me!
pow smackapow!
haha now you'll lose!
deker:is that a butterfly! :D
Intense wrestling! Marshmllo vs Superhot fire!
Nuuuu he spit fire at me :'(
-------------------------------------------
Here's My Canada: No Corrupt Government - Duration: 0:08.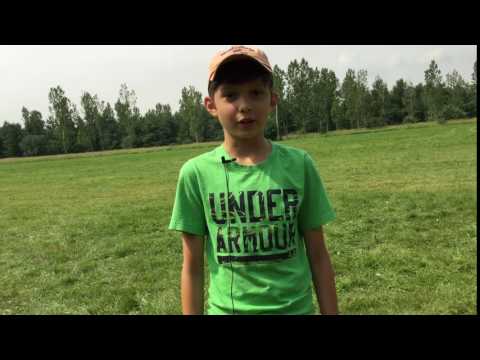
I am proud to be Canadian because we don't have
a corrupt government that takes everything from us.
-------------------------------------------
Here's My Canada: Free and Beautiful Land - Duration: 0:12.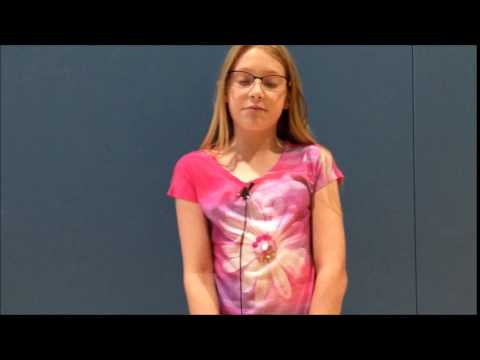
I'm proud to be Canadian because we
have so much free and beautiful land.
I'm also proud to be Canadian because
my favourite singer Sean Mendes is Canadian
-------------------------------------------
Here's My Canada: Proud to be Canadian - Duration: 0:16.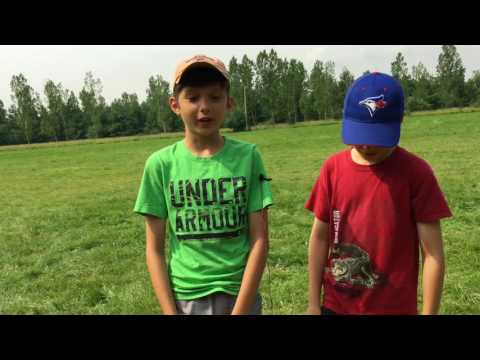
I'm proud to be Canadian because our government
provides what we need to live.
I'm proud to be Canadian because we don't have to
wake up every morning worrying about having to go
through the next day.
-------------------------------------------
Study One of the Keys to a Happy Life is Being a Generous Person - Duration: 3:49.
Study One of the Keys to a Happy Life is Being a Generous Person
By Seth Pollard
Let�s be honest for a moment.
You�d probably be thrilled to have a cool million or 2 in the bank.
Money can�t buy happiness, as the saying goes, but what you do with your money (as
well as time and talents, for that matter) might have an awful lot to do with your quality
of life.
Sure, doing something nice for someone else feels nice, but a recent study suggests that
generosity has a positive biological effect on the brain.
For the study, published in Nature Communications, researchers at the University of Zurich in
Switzerland told 50 people they would receive $100 over a few weeks.
The team asked 25 of the individuals to use the money only on themselves, and asked the
other 25 participants to spend it on someone they knew.
The researchers wanted to know: Would the mere promise to spend the money on someone
else be enough to make people happier?
Before handing out the first batch of cash, the researchers brought those in the give-away
group into the lab and asked them to think about a friend they�d like to give a gift
to and how much they would hypothetically spend.
Then, the participants underwent functional MRI scans so researchers could measure activity
in 3 regions of the brain associated with social behavior, generosity, happiness, and
decision-making.
Those who had pledged to spend the money on other people were more likely to make generous
decisions throughout the duration of the experiment, the team found, compared to those who had
pledged to spend the money on themselves.
The group�s MRI�s showed more interaction between the parts of the brain associated
with altruism and happiness, and the participants expressed higher levels of happiness after
the study ended.
Furthermore, it didn�t matter how generous people were.
Even giving away a small amount of cash impacted the participants� happiness in the same
way.
Lead author Philippe Tobler, associate professor of neuroeconomics and social neuroscience,
said:
�At least in our study, the amount spent did not matter.
It is worth keeping in mind that even little things have a beneficial effect � like bringing
coffee to one�s office mates in the morning.� He added:
�You don�t need to become a self-sacrificing martyr to feel happier.
Just being a little more generous will suffice.� [2]
Co-author Soyoung Park says many questions remain unanswered.
[3]
�There are still some open questions, such as: Can communication between these brain
regions be trained and strengthened?
If so, how?
And, does the effect last when it is used deliberately, that is, if a person only behaves
generously in order to feel happier?� Earlier studies have shown that older people
who are generous tend to be in better physical shape.
Some research has even suggested that spending money on other people is as effective as medication
or exercise for lowering blood pressure.
[1]
So the next time you feel like treating yourself, consider treating someone else instead.
It might make you feel even better.
Tobler said:
�It is worth giving it a shot, even if you think it would not work.
In order to reap health benefits, repeated practice is probably needed so that giving
becomes second nature.�
-------------------------------------------
Here's My Canada: We Help People in Need - Duration: 0:07.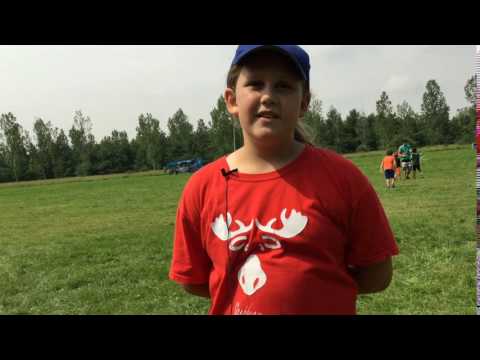
I am free to live in a place that is safe
and help people in need.
-------------------------------------------
Here's My Canada: Mixed Culturally and Religiously - Duration: 0:08.
I am proud to be Canadian because we are very mixed
culturally and religiously.
-------------------------------------------
Isuzu D-max 3.0 LS Automaat - Dubbele Cabine - Grijs kenteken - Duration: 1:01.
-------------------------------------------
Photo Etching – Professional Tools for Modelers - Duration: 15:33.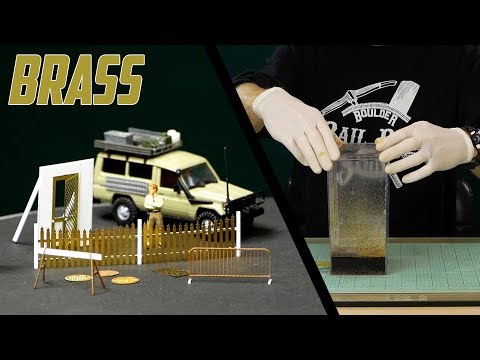
When most of us think of photo etching we think of very small packages at the hobby
shop that cost a fortune for a few small pieces!
But with a very small amount of knowledge you'll soon discover making and using your
very own photo etched parts is much easier than you think.
Let's not waist any more time and get started with the tutorial
The hardest part of this whole process is designing something to etch, at a bare minimum
you can use a program like Microsoft Paint however if you use a program like Adobe Illustrator
or something similar you'll be able to get much better designs.
There's just a bit of a learning curve to using a program like this but the results
are worth the time spent learning the program.
For this tutorial I'll be using the Photo Etching kit from Micro-Mark called the Pro
Etch System, it comes with everything required however if you live overseas you'll need
to purchase the etching chemicals locally from your country.
Supplied are two clear sheets for printing on, before using them make sure they are free
from fingerprints and dirt as this will affect the quality of the print.
One side is ever so slightly duller than the other but it was very difficult to tell.
If you're struggling to figure out what side to print on just grab a high lighter
and draw a small dot in one of the corners, if the highlighter ink rubs off then you'll
need to flip the sheet over, if the highlighter ink doesn't rub away then you have the correct
side for printing. And now we're ready to print
Make sure that all the print settings are set to their highest quality and if you printer
has the option, adjust the color to ensure it prints as dark as possible.
After printing just let it sit aside for 10 minutes to ensure the ink is completely dry.
If you're tempted to try overhead projector clear sheets let me save you some time and
money!
On the left is a projector sheet and right is the micro mark clear sheet.
They both look great right… let's get a closer look.
The micromark sheet looks nice and crisp and the projector sheet in comparison looks terrible!
The ink is uneven, blotchy and more translucent compared to the smooth, sharp and even micro
mark sheet.
Any spots or imperfections can be touched up with a sharpie.
When cutting out the templates leave a fair bit of overhang in the sheets except for the
top sheet, the top sheet needs to be taped to the bottom sheet and this is much easier
if one sheet is bigger than the other.
It's easier to register the template by first taping the bottom sheet to something
white, in the pro etch kit you'll have a sheet of white styrene that does a perfect
job for this.
Just make sure the ink side is facing up on the bottom sheet, now with the top sheet make
sure the ink side of the sheet is facing down and line it up with the bottom sheet.
So the two inked surfaces of each sheet will be touching.
Take your time lining them up, the closer to perfect you can get them the better your
final etched piece will be.
Also just remember that these sheets are not waterproof and if they get any drops of water
on the inner surface they'll be ruined.
So keep them dry.
With everything lined up you can tape the top and bottom sheets together.
You only tape 3 sides so we create a pocket for our metal sheet to slot into.
Now we can remove it from the white sheet, trim away the excess and put it aside to be
used later.
The pro etch system comes with a .005 inch sheet of brass and a .005 inch sheet of stainless
steel, I'll be using brass for these etches.
Cut a piece of brass so it will fit inside the pocket and if you use scissors remember
to flatten out and kinks or bends.
Next I'll cut some photo resist to fit over the metal, It's safe to open the UV sensitive
resist under normal room lighting for a few minutes however to be on the safe side I dim
the lights to preserve the life of the roll.
You'll need one for the top and bottom of the metal.
While I continue to prepare the metal I store the two small pieces of photo resist in a
dark box until I'm ready to apply them.
The metal needs to be polished, simply use the supplied polishing pad.
As you can see at the moment when water is dripped onto the brass it beads up.
To polish dampen the polishing pad with some water and rub back and forth on the metal
in the direction of the grain until the water no longer beads ups but instead evenly spreads
across the surface.
Both sides need polishing and once done rinse the metal with water, try to avoid touching
the top surfaces.
Handle from the edges to avoid getting finger prints on the surface.
Now we can apply the photo resist.
The resist has a protective cover on both sides, one side will peel away much easier
than the other and to do this you'll just need a piece of celo tape and gently peel
revealing the corner.
If you're having trouble you can use two pieces of tape one on each side of the same
corner.
The metal is still wet from cleaning which is what we want, gently place the resist over
the metal and lightly press and rub along the resist.
This will help remove the excess water from between the metal and the photo resist.
Then do the same for the other side of the metal.
In preparation for laminating the metal is placed between two pieces of carrier sheet,
the carrier sheet has a shinny side and a dull side, the metal gets wedged between the
two shinny sides and the dull side should be facing out.
If you're like me and live in Australia you'll need a 110v power source to plug
the laminator into, now we just wait a few minutes for it to heat up.
Now that it's ready we just feed the metal in-between the two carrier sheets through
the laminator, on the second pass we just flip it over and rotate 90 degrees.
Check that you have no bubbles and we can move on…
If you have any bubbles you'll need to strip the photo resist back and start again.
To expose the metal we place it into the template pocket ensuring that it's centered, to make
sure we get nice crisp lines from the exposure we'll need to place the template and metal
in between two pieces of Perspex and clamp tightly from all for sides.
Everything here is all supplied in the kit.
The light I used for exposure is a Nelson portable security flood light and a 100 watt
Philips 100w Clear Edison Reflector Globe, its set up to be 17cm above the table and
about 15cm away from the top surface of the Perspex.
It gets pretty warm so I wouldn't set it up any closer than that.
I set my timer for twelve minutes and go drink a coffee, it will gradually turn a medium
purple color and once the time goes off I flip the plate over and cook on side two for
another 12 minutes.
If you're wondering why 12 minutes it's from doing a few test pieces.
I did one at 10 minutes and it wasn't enough another I did for 15 minutes and some of the
black areas started to become exposed so 12 it was!
To develop and remove the unexposed photo resist I simple use washing soda.
I mix a rough 1% mixture into 100ml's of water.
It doesn't have to be perfect, this stuff is pretty forgiving.
As long as it's close.
Before we dunk out metal into the washing soda we need to remove the final protective
layer.
Again with a piece of sticky tape press it on one corner and peel it back.
You should see a clear sheet being removed.
Do this on both sides.
Drop the metal into the developer bath and gently brush the surface for about 2 minutes
on each side or until all of the unexposed resist has been removed then rinse of in clean
water.
You should be able to see clear edges around your pattern, as if your design is a sticker
that has been pressed on and the metal should look clean.
It's hard to tell on camera but when you look at it and touch it with your own hands
you'll know.
The etching tank is prepared following the supplied instructions, it's pretty straight
forward.
The metal is press into the clip and test fitted into the tank.
To etch I'm using hydrogen peroxide, and I'm using hydrochloric acid.
Because the etchant we're making is highly corrosive you'll most certainly want work
in a well ventilated area and you'll need to use skin and eye protection.
To calculate exactly how much etchant I'll need to mix up I firstly fill the tank with
water up to the desired level, next I weigh the water which in this scenario was just
over 240ml, so know I know in order to mix a 2:1 ration of 2 parts hydrogen peroxide
and 1 part hydrochloric acid I'll need a total of 160ml of hydrogen peroxide and 80ml
of hydrochloric acid.
Were ready to start etching.
Insert the metal that's attached to the lid and turn the air pump on.
Leave it for a few minutes then remove it from the tank give it a quick rinse and remove
it from the clip and rotate it 180 degrees and put it back into the tank again.
I repeat this process about 3 or 4 times.
The side that is pressed into the clip tends to etch slower from that side which is why
we need to rotate it on the clip a few times during etching.
Once it's finished remove the parts from the tank and give them a thorough rinse in
water.
Some bits broke away but that ok.
You may fine some parts are fully etched but others needs just another minute, this is
easily done by removing that part that needs additional etching and placing it a small
container with some of the etching fluid in it.
Gently swish the etchant around until the part is fully etched.
It's possible to do an entire etch in a small container from scratch, I found by elevating
the piece in the container helps get a more even etch however it takes a little bit longer
over all to etch and you'll need to continuously agitate the fluid during the etch.
Just mix up the same ratios of hydrogen peroxide and hydrochloric acid and watch your design
come to life.
Remember to carefully dispose of the etchant solution once you're done, I put mine in
a spare bottle and once it's full I'll take it down to the local waste facility that
can handle these materials.
To remove the rest of the photo resist I roughly mix a heaped teaspoon of washing soda in with
water, after mixing I just place the parts into the water and leave it to soak, after
15 or 20 minutes the resist will just float away revealing the completed pieces.
Now they just need a good rinse in clean water and we have our finished pieces.
I use a good pair of scissors with a very fine tip which is perfect for cutting these
very small parts and you'll also need some small files to clean up the edges.
Here you can see the difference between a 0.015 inch thick pieces of copper and a 0.005
inch piece of brass, you'll soon discover if you have a design with very fine detail
you'll get better results using thinner metal rather than the thicker metal as you
can see from the fine tips on the fence.
The brass on the left has retained the detail while the thicker copper on the right has
rounded tops and it looks overall a lot softer around its edges.
To add these to my models and glue them to plastic I find using CA glue and a pin works
just fine.
That completes the tutorial, you should now have no trouble designing and etching your
very own metal parts to add insane amounts of details to your scenes.
If you are enjoying these video and you'd like to help support the channel feel free
to check out my patron
-------------------------------------------
PROTOTYPES & PLANS : SkyPacks iRedstone Elytra Reality & Camo Resource Pack Module Minecraft | ☿ - Duration: 6:43.
Hello, Meri here, welcome to the first "Texture Thursday" episode, yes, on a Friday, I'll explain that later ;)
"Texture Thursday" is a casual overview about what I'm up to regarding resource packs,
in this series you'll see prototypes of new module additions, sneak peeks / spoilers, as well
as well as releases of alternative types or colours of already published modules.
I highly appreciate feedback, even more so on not yet released prototypes, so maybe
I implement your input into it before I release a module, a bit of interactivity with you
would be really cool \ö/ :D
Yeah, speaking of "new module prototypes", generally speaking - and I'm not overexaggerating -
there are literally THOUSANDS possible modules including variants that I can think of to do
It'll be at least interesting even for those amongst you who usually don't use any packs
at all, or a completely different style.
You will still enjoy at least the idea and presentation itself,
I put all my Love and Heart into it, as always ;)
iRedstone.
A module that is a tool for technical players, the 3D clean, modern, "LED cable look" redstone
dust, of course, is part of that pack.
This pack is a matter of my heart, I work on that with great care since very long,
I just don't show much of it publicly ;) - yet ;))
As you might figure from the logo graphics, I plan on 2 different iRedstone packs, one
is a default- or faithful-looking module, the other one will be modern, clean, both
packs will be high-quality of course.
For the iRedstone Default pack, there will be a few exceptions to that Faithful approach,
for example I will also make the Redstone wire look "clean", unlike Default, but it
will be very flat, you can see here in the comparison picture the already released iRedstone
modern Redstone wire with the planned Default Redstone wire, and for height comparison an
iron pressure plate as well.
So, a really really flat wire for the iRedstone Default pack, but still a model, not just a texture
Still a prototype, like I said, I go about that with great care, I always put a lot
of thought and love into my creations :)
Elytra Reality.
You can get wing type 0001 in currently 3 colours, I plan to release this wing type
also in Black as well as White, I'm currently still experimenting with a Dark Purple and Blue
I will let you know in future "Texture Thursday" episodes when and which colour variants
will be released, and where you can get them.
Elytra Reality wing type 0002 will be more simplistic-looking, of course high-quality
textures, but the style will be very subtle, compared to Elytra Reality wing type 0001.
So definitely something for those who prefer a more simplistic and realistic over a somewhat
"magical dreamy" look ;)) And, of course, I also plan on various different
wing types, and not solely those of real or fantasy creatures.
Just wait and see ;)
Elytra Camo: There will be at least 3 more Captain America shield types, but before
I work on those, there's another Superhero that will get a Camo-Elytra.
- Who do you think will be next..?
I'm curious how many of you will get it right, let me know which Superhero, and why you think
they will get a Camo as next one ;)) Of course, feel also free to suggest a new
Elytra Camo type, also for Super-Villains, I already got many Camos planned myself, but
you can come up with something I haven't thought of yet!
On a personal sidenote: I started to learn reading with Superhero comics and also Mickey
Mouse, I'm a huge fan of that genre, and thus will work on those with great passion and love!
Yeah, I really very much enjoy doing these, as it's part of my real life hobbies, but
I will talk about that in my ChillTalk series sometime, and someday I also might even show you
in a Vlog some of my action figure collection }xD
ELYSION
Under this handle I plan to offer you high-quality - and I really mean it.. -
*HIGH* quality - SkyPacks in the future!
Some of you may already know that I'm into Astrophysics, Astronomy has been the first
science topic I loved when I was just a few years old due to SciFi like Star Trek and
Star Wars, and I'm a huge fan of Sci-Fi, generally, so you can expect beautiful - or I should
rather say: stunning-looking SkyPacks coming from a Space nerd and Sci-Fi geek like me :)
While I'm talking, you already saw some little sneak peeks, some rough sketches.
There will be realistic-looking SkyPacks, but also some that will be purely for visual
enjoyment, not really realistic at all, for example with a bunch of visible planets or
planetary objects etc., which I will, for the most part, create myself, you can see
here some prototypes of planets and moons, asteroids, etc.
Of course I'll also partially rely on some footage of NASA and other space institutions,
but I want to create *unique* SkyPacks for you and not only take some images from the
internet, that would be too easy and not very original, like I said, I want to do the best
I can for you, and that naturally involves myself as a creator or artist.
There won't be a "Texture Thursday" episode each week, my Youtube content does not only
focus on resource pack modules, and I'm also very busy in real life as well as
"behind the scenes", and, generally, yeah, my type of content needs a lot of time to be prepared,
no generic-easy-to-do content :)
So, why "Texture Thursday" on a *Friday*?
;) Well, there will be "Texture Thursday" videos
where I won't talk at all, just release some additional variants of already showcased modules,
or showcase some prototypes, and those are the videos that will be published on Thursdays,
5pm UK time, with just text overlays explaining everything.
But if there's any information like in this video, where I can't really explain everything
to you just via text overlay, of course I will make a "talk'y" "Texture Thursday" episode
like this one, which will then usually be released on _Fridays_, as recording with voice
needs way more time, and I need to work }=/ };]
Take care, enjoy life. ☿ Meri ❤
No comments:
Post a Comment