Hey !
A little bit of talking before the video begins, if you want to skip this, I'll put the timecode here
1:30 bro
So this is a new emission, that I simply named "Special Edition" (don't know if it really has the same sense in English tbh)
I choosed this title because first, I lack of imagination for that, and
because as you can see they are not "real shurikens", they are hand spinners
so they are not really "props"
And why a do I make a "new emission" ?
because the next prop is taking me a lot time to make
really, a lot of time, trust me
Spoiler alert, an image of the prop coming
So I'll be making these kind of short videos if the props are too long
So that you will know that I'm not dead
It will often be 3D printed stuffs because it's really quick for me to do that
Well, a new emission goes with a new opening, so let's go
So, lots of weeaboos among you asked me to make the Genji's Shurikens
So I didn't make them
Seriously, there are lots of great videos on youtube dealing with that, just look for them, they are great. Really.
So I think we're ready to make the hand spinners, this is easy and quick, don't worry
So I must say that I didn't make the 3D models
But the links are in the description of the video
If you don't have any 3D printer, just calm down, ask a friend, your family, or website on internet
Or just ask me and maybe I'll do it
maybe ...
To make to shuriken spin we'll need a ball bearing
You can find that on rollerblades, or internet, or hardware shops
Before printing, reshape your 3d model to be sure that the ball bearing fits just well
or else it won't work, obviously
And to be sure, that it stays, I used epoxy glue, but you can use super glue
be careful to put glue on the exterior edges
Once the printing is done you can sand it, and what I like to do is to gently rub some acetone with a cotton bud
and don't put too much acetone or it will disolve it
So yeah, here it is, we're almost done, just paint it
As I told you, it's a short video!
But if you're new to this channel, well you can subscribe, I have more consequent work, don't worry
So that's all for this video
And That's it for me guys, see you !
For more infomation >> [3D PRINTED] Hand Spinner Genji's Shuriken - Duration: 3:25.-------------------------------------------
Ep 37 - Greece (part 4) - Around Europe on a Motorcycle - Honda Transalp 700 - Duration: 14:09.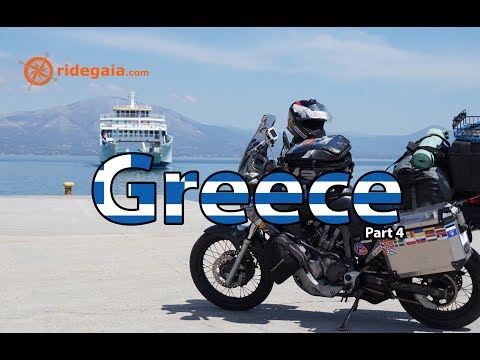
One year on the road is a fact!
I was in Athens, where I made a big service to the bike.
I was staying again with good friends, Manolis and Apostolis and we got to do some things together.
- What do you want me to say? The guy didn't stop.
- One, two.... - There is the thrird and the fourth on the other side.
He was going fast and he crashed everything....
Well, he didn't stop. He must have been from Gargalianoi
We are waiting for the police to find a solution.
Today is 3 of April, and that means that tomorrow I complete one year on the road.
And for that reason we are going to cook Seftalies! (Cyprus Traditional food)
-This is for you!
- Thank you!
I want to thank X-power motorcycle service and the owner Giorgos Karderinis for the bike service.
The bike feels perfect! Like its brand new!
I want to thank Andreas Psyhogios as well for taking the initiative to equip my bike with brand new tires.
I left Athens and headed to Oropos to visit a very good friend of mine.
We didn't see each other for more thann one year, since I left Cyprus.
I stayed there for a couple of days and then I continued my trip to check out Euboea.
Good morning!
I am in Oropos and I am about to take the fery to visit South Euboea...
and afterwards, I will make a round to check out North Euboea as well.
I am in Karystos...
I was riding till late and I reached a small village called Amygdalia.
And I met Mr. Costas and Mr. Panagiotis, his brother.
I was asking them if there is a shop to buy food.
My plan was to get some food and pitch my tent In a small church I found before the village.
When they hear that they invited me to stay at their place.
They cooked for me something to eat.
They are very good people.
I pitched my tent the front yard...
The only thing that he owns is a small room with dimentions 2m X 3m.
There is only a bed inside and a small table.
He doesnt even have power....
Not even a toilet!
Good morning!
It's 7:40 am...
I woke up at 6:30 today...
I am in Amygdalia Village in South Euboea.
I rached this place around 7 pm
and I fount out that the rest of the road to reach my destination
which is the canyon of St. Demetrios, it's a dirtroad.
So I desided to come down to the village to find something to eat before pitching my tent.
And I met Mr. Costas and his brother, Mr Panagiotis
They are the 2 of totally 7 people of the village.
And they invited me in their place.
Accross is the island of Andros.
Mr. Costas with the little that he owns tryied to be as generous as possible and I really thank him for that.
He has a very small room that he lives in and right next to it, there are his farm animals.
Some dogs, some sheeps and some goats.
He told me to sleep in the room, but It couldn't just invade his space,
so I told him I would be fine, if he let me pitched my tent in his front yard.
He fryed a potato and 3 eggs for me.
He did things that, very rare people do for a stranger.
To understand how poor he lives, he doesnt even have a toilet.
He told me that if I want to go to the toilet just grab some parer and go whereever you like!
"We are free over here" he said.....
I have a 25km of dirtroad....
I am in St. Demetrios canyon.
There is a small cantene that it's closed.
I guess that I am here "out of season"
I passed the bike on the other side from there...
which i misscalculate it a bit.
Thankfully I didn't drop the bike.
But this is deeper than it looks and the rocks are slippery.
I was trying to hold the bike with my legs at a point and the water reached up to here.
So the plan is to pass it from the bridge this time.
The bridge looks pretty solid.
The bike can fit through it as well.
That was the double stand. If that double stand had a mouth it would curse me.
I continued to North Euboea...
The landscaped changes there. From rocky with low vegetation becomes more
"green", with higher vegetation.
I am in North Euboea. Just arrived to Ayian Anna beach and here is where I will camp tonight.
I am at Ayia Anna beach and the moon just rise up and its totally red..
After cheking out Euboea, I took another ferry to mainland Greece and I continued to Levadia....
-------------------------------------------
ASEAN summit ends without statement on S. China Sea - Duration: 0:46.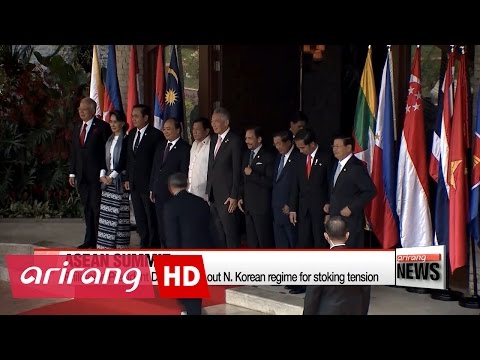
Leaders of the Association of Southeast Asian Nations, or ASEAN, wrapped up a summit on
Saturday amid heightened tensions on the Korean peninsula and the South China Sea.
According to reports from Manila, the summit ended without a customary joint statement.
It was unclear whether there was agreement among the members over China's military fortification
of several disputed islands in the region.
Statements by ASEAN typically do not mention China directly.
But the chair of the meeting, Filipino President Rodrigo Duterte, did address the problem of
North Korea's provocations, saying the regime's leader Kim Jong-un wants to "end the world."
He also held a phoner with his American counterpart, reportedly urging Trump not to be provoked
by the North Korean regime.
-------------------------------------------
U.S. Pres. Donald Trump emphasize China's role in reining in N. Korea - Duration: 0:45.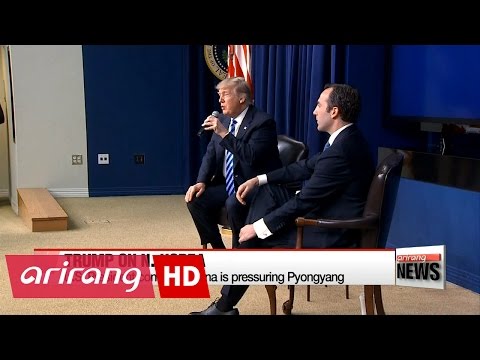
U.S. President Donald Trump expressed confidence that China is stepping up to the plate to
do more in resolving North Korea issues.
During an interview with CBS News, though full of ambiguous responses, the former real
estate developer did say, "We will not be happy if North Korea conducts another nuclear
test", a U.S. military response is not being ruled out for such provocations, and that
"we'll see."
When asked if the measures against Pyongyang are not working since the regime launched
another missile on Saturday, Trump explained he has grown to like and respect Xi Jinping,
that he believes the Chinese leader has been pressuring his North Korean counterpart.
The former reality show star downplayed the hermit kingdom's failed missile launch, calling
it an expected move, and that it was a small missile.
-------------------------------------------
Annual S. Korea-U.S. joint military exercises end - Duration: 0:42.
Seoul and Washington complete their Foal Eagle exercise on Sunday.
The 2-month-long annual joint military drill involved some 300-thousand South Korean soldiers
and 10-thousand U.S. troops.
Though it is purely defensive in nature, tension mounts during the combined training as Pyongyang
perceives it as a preparation for an invasion.
The U.S. aircraft carrier Carl Vinson meanwhile, is still taking part in a different joint
exercise with the Korean navy that began on Saturday... expected to end some time this
week.
The Nimitz-class supercarrier that took part in drills last month and had left the area,
but was called back, seemingly in response to North Korean provocations.
-------------------------------------------
April Reading Wrap Up | 2017 - Duration: 14:46.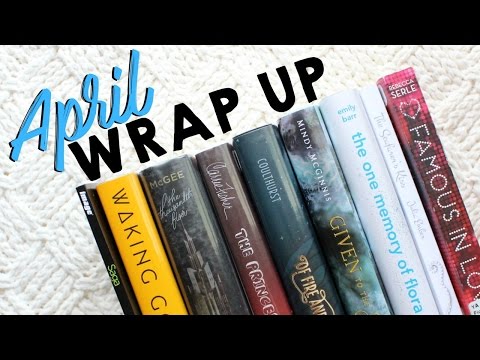
[music only]
Hi guys! It's Trina and this is my April
reading wrap-up. All the books that I
read this month were included in that
introduction so that you can have an
overview of the reviews you can expect
me to be doing in this video,
and there are timestamps in the
description in case there is one book
review that you want to jump straight to.
And I also always put Goodreads links to
all the books that I talk about in my
videos in the description so that you
can easily find those books. I'm going to
jump right into my TBR check in now, so
this month I planned to read these four
books and I did terribly this month. I
only had four books on my TBR and I read
two of these... yeah. I don't really have a
lot of excuses for that, I was just in a
really weird reading mood this month and
also my copy of The Circle, like the day
after I made my TBR video a bunch of
people got in line for the book at my
library and I had to turn it back in. So
I just have not been able to keep a copy
of The Circle in my hands. So, I haven't had a
chance to read two of these books yet
but I still really do want to read them
eventually. This month I read a total of
nine things. Four of them were print books,
four of them were audiobooks, and the
other one was a comic bind up. I'll get
into reviewing these books now, and like
always I am going from my lower end of
my rating spectrum to my highest end,
finishing up with my favorite book of
the month. So first of all in April I read
Saga volume 7 written by Brian K. Vaughan and
illustrated by Fiona Staples. This is a
comic series and this is a sci-fi
fantasy set in space. It is about
this intergalactic war that is happening
and these two people from different
sides of the war have fallen in love and
run away together and they've had a
child together. This is really frowned
upon by both sides of this war so both
of their races are hunting them down.
It's just a really epic space fantasy
and I do enjoy the story of this series.
There is a lot of graphic nudity, very
graphic nudity, so heads-up on that. This
volume itself, I just felt like not very
much happened. We spent this entire
volume like very stationary in one place,
a long amount of time
happened with not much story to really
show for it, so I just didn't feel like
this one was the most exciting of the
volumes in this series. Next up, also at
three stars, I read The Thousandth Floor
by Katharine McGee. This is a YA
sci-fi book that reads very much like a
contemporary. It is set about a hundred
years in the future where New York City
is no longer a sprawling city. Instead,
they have built one tower and everyone
in New York lives in this tower. The
higher up in the tower that you live, the
richer you are, the more popular you are.
This book has five different points of
view so there are four female characters
and one male character and I actually
thought that it was pretty difficult a
lot of times to keep all four of the
female characters separate, especially
three of them. They're all these girls
that live on the upper floors, they're
really into parties, they're friends with
each other, they're in a lot of scenes
together, and I just like could not keep
up with which character was which one.
Like, their voices and their story arcs
didn't really seem that distinct at
times. And then around the time I got
about halfway through it, I was like, 'okay
I'm invested now. I really want to know
what these people's secrets are,' and
stuff but this is definitely a story
that is all about secrets, and lies, and
drama, and frenemies. I feel like you would
like this one if you like Sara Shepard's
books, like the Pretty Little Liars
series. And I have seen a ton of reviews
comparing this one to Gossip Girl but I
have never read or seen Gossip Girl so I
can't really tell you that. I did enjoy
how all these characters' storylines wove
together and like the amount of
blackmailing that went on here. Like, there was
just a lot of secrets, so there is a bit
of intrigue to this one. There were two
books that I gave three and a half stars
to this month and the first of those was
The Seafarer's Kiss by Julia Ember. This
is a YA Little Mermaid retelling inspired
by Norse mythology and in it our main
character is a mermaid and she lives in
this underwater Kingdom and they kind of
have this idea for the life that she
should be leading but she's not really
interested in their plan. She doesn't
really want to mate with the Merman that
everyone expects her to be with and
instead she ends up falling in love with
a human girl who is a survivor from
a recent shipwreck. The main
character in this one is bisexual and
that is own voices representation. The
main character is also fat, so there is
some fat rep in it but I myself wasn't a
big fan of some wording of some of the
fat rep. And there is also a non-binary
side character that uses they/them
pronouns. This book actually does not
come out until May 4th but I was sent an
early copy of it in exchange for an
honest review. I do already have a full review
video up on this book which is non
spoiler. It is a review and a discussion
if you guys want to hear more of my
thoughts. But my brief overview of this
is that I thought it was a fantastic
retelling. It was true to the original
story while still leaving a lot of room
for surprises. It twists the retelling a
little bit. What I was not a fan of was
the romance because there is physical
violence portrayed between the two main
love interests that kind of isn't really
addressed. The other book that I rated
three and a half stars this month was
The One Memory of Flora Banks by Emily
Barr. This one is a YA contemporary about
a young girl who she had a brain tumor
and at 10 years old she underwent an
operation to remove the tumor but it
left her with a form of amnesia. She
remembers everything up until the moment
she had that surgery, so she remembers
being 10 years old but now she is 17 and
she has not made a new memory in the
past 7 years. But then one morning she
wakes up and she has a new memory from
the night before. She can remember being
17 now, and she remembers kissing her
best friend's boyfriend, and Flora thinks
that kissing him healed her brain and her
memory. This book is also not coming out
until May but I did read it early
because Penguin Teen kindly sent me a
copy of this one so I can do a video
about it. So I will be having a review
and a themed video about this book
coming up soon, but my overall thoughts
on this book are that at first I was
very put off by that idea of the love
interest "curing" her. That is something
that is mentioned in the book summary on
the book jacket, but I will say that the
book makes a point in the end to show
Flora that that is not the case. I also
had a hard time getting into the
writing style because it's very
simplistic and it's very repetitive but
as the book went on, again I noticed that
the writing style started to improve and
so I think that this was really done in
that specific style to portray the
mental state of Flora. What I really
liked about this book is that there was
a sense of urgency and mystery that was
portrayed through the writing and that
is something that ended up really
gripping me and just propelling me
through the book. Like, I stayed up way
too late reading this book because I
could not put it down. I do want to give you
a heads up for some content that is included.
I would argue that there is an abusive
parental situation happening here and
there are also a couple of scenes of
self-harm, either on page or Flora
thinking about it. So just a heads up for
that content, but overall I enjoyed this
book a lot more than I initially thought
I was going to so three and a half
stars feels like a good fit for this one
for me. There were four books that I gave
a four star rating to this month. First is
The Princess Diarist by Carrie Fisher.
This is one of Carrie Fisher's memoirs.
She just recently passed away like just
a few months after this books came out
and that was actually the reason that
kind of prompted me to pick this book up.
I was just really sad about it. And I
listened to this one on audio because it
was a memoir and she does narrate this
audiobook herself. And in this book she
is just reflecting on her time working
on the first Star Wars film. She talks
about just herself before the role of
Princess Leia, during the role of
Princess Leia, and after that, and how
Leia really affected her life. She talks
about how much she appreciates this
character. Like so many other people, I
grew up on Star Wars and Princess Leia
was a really great female role model
in film for me, so that was why I was
interested in this one since it is
specifically talking about her
experience with Star Wars. It was
difficult to listen to this one at some
points because Carrie often like
wonders what people will think of her
after she's dead, and so with that being
so fresh it was just kind of difficult
to read at times. But I do think that
this one would be one I would suggest if
you enjoy celebrity memoirs or if you
really love Star Wars. I also read Given
to the Sea by Mindy McGinnis, which is a
YA fantasy about a world in which
everyone lives on an island and the
ocean level is rising, and the way that
this culture combats the ocean is they
believe that if they feed a girl to the
sea it will be appeased and it will
leave the rest of them alone. So they
sacrifice one life to save the rest of
the world. Now, the girls who are being
thrown into the ocean are from one
bloodline so they have to produce an
heir before they can become the
sacrifice and this generation's girl
that is given has not yet had a child.
The ocean that seems like it's getting
angrier and all the people on this
island are getting much more restless.
They're starting to go to war in order
to control the safest spot on land.
I liked the world and the world building. I had no
trouble getting into this. In fact I
was reading it thinking, 'wow that was
really easy to get into this,' and you
know, it's Mindy McGinnis's first
time writing fantasy so that was
something that I was kind of wondering
about. This is definitely something that
deals with much more adult, darker themes
because Mindy is a writer who always
deals with the darker themes of humanity.
The main thing that she is tackling in this book
is rape culture and I think that if you
enjoyed her book The Female of the Species
you'll also enjoy this one. Also, because
this one deals with rape culture there
is one scene of an attempted rape. There
are definitely some scenes that were
tough to read and I do think that this
book will make you kind of uncomfortable
so it really just depends on what you're
looking for in a fantasy. If you are a
fan of romantic fantasies with a lot of
fantasy creatures and magical systems
this is not really going to be the
series for you, but if you like things
that are less magic based and more about
the politics then I think that this one
will appeal to you. I am planning to do a
full review video on this book because I've
read everything by Mindy McGinnis and
a lot of you guys have asked me to
please review this one. I will be
putting that up soon so stay tuned for
that to see more of my thoughts on Given
to the Sea. Next, I read Famous In Love
by Rebecca Serle, which is a YA
contemporary romance. This one is about a
girl in a high school drama class who
wants to be an actress and she goes and
auditions in an open casting call for
the lead role in this big movie that's
being made that's adapting a set of
books that are like bestsellers. They
have this huge fandom around them. She's
a totally inexperienced actress but
she ends up landing the lead role and she
is thrust into fame overnight. And as she
starts filming the movie she finds
herself getting involved in some of the
romances that her book character is
involved in in the story. I heard about
this one because it's being adapted into
a TV show, so this is a book about a book
being adapted into a movie and this is
all being adapted into an actual TV show,
so it feels like book to movie
adaptation inception is happening
here. But I heard about this one because
Freeform is starting the TV series of
Famous In Love based on this book and I
recognized the name Rebecca Serle
because I have read another of her books
before and I did enjoy it and I've
always been meaning to read something
else by her so I thought this is a good
opportunity. I can read the book and then
watch the show, and I have seen the first two
episodes of the TV show now and I did
enjoy them. I liked it a lot more than I
thought I was going to.
It is very fluffy, cheesy romance. I just
got to a point where I was like
addicted and I had to know what was going to happen.
I felt really wrapped up in this story
for a little while so I did enjoy this
one overall. And my other four star read
of the month was Of Fire and Stars by
Audrey Colthurst. This is a YA fantasy
romance. It is about a princess who has
been betrothed to the prince of a
neighboring Kingdom and when it's time
for them to meet she goes to his
kingdom and meets him, but she ends up
falling in love with his sister instead.
So she's bisexual and that is own voices
representation and this is a romance
between two princesses. I did feel like the
world-building in this book was maybe a
tad bit underdeveloped because I didn't
always understand who the different
nations were and who was allied with who,
but I was really intrigued by this story
and it had a lot of things I really
liked about it. The romance was good.
There's a really solid mystery that's
happening throughout the book which I
did not expect and that really kept me
interested in the plot. I did enjoy the
setting with the world itself, even
though maybe some of the background and
politics could have been fleshed out.
I really really enjoyed the characters. I
really loved that the two princess
characters are kind of opposites, like
they balance off each other really well.
And our main character is a nerdy
princess. She loves studying things, and
knowing facts, and she loves being
involved in like their politics. Another
thing I liked about this world was that
it was not a heteronormative world. A lot
of the characters were in like same-sex
relationships or they liked multiple
genders and nobody really batted an eye
at that, like that was just kind of the
norm. I really enjoyed this book. I think
some of the plot and some of the world building
felt a little bit rushed, but I loved the
characters, the romance, and the mystery so
I definitely want to read more by this author.
And lastly, my favorite book of
the month was Waking Gods by Sylvain Neuvel.
This is the sequel to Sleeping
Giants and this is an adult science
fiction series about people who have
uncovered these giant statues and when
they put them all together it makes up
one human looking figure, but it isn't
quite human, so they're trying to figure
out what this thing is, what does it do, and
where did it come from? This story is told in an
interview format. Like, everything in the
book is pretty much all audio files. You
have some radio news reports, some audio
interviews that have been recorded
between characters, some audio of
personal diaries that the characters
have recorded. So this series actually
works very very well in the audiobook
format if you want to listen to it
instead. It is narrated by a full cast
and I just think it is so enjoyable. It
is very similar to the Illuminae series
in that relation but the book itself is
not as highly formatted visually, and the
stories are completely different of
course. This was absolutely my favorite
read of the month. I just got to the
point where I was like 95% done with the
book and I just had to put it down
because I was not ready for it to be
over. I love spending time in this world
with these characters and trying to
figure out what is going on and Sylvain
Neuvel always writes these really weird
plot twists right at the end of each of
the books and you're like... WHAT?
How did that happen?! And then you have to wait
for the next book and just, the next book
is going to be so totally different
because things have changed now. I can't wait for
the sequel. I just geek out over the series. I love
it so much. I just highly recommend this
series and definitely the audiobook
version of it. So those are my reviews of
the nine books that I read in April. If
you have any questions about the content
or anything about these books that I did
not cover in these revies, please ask
me that down below and I will answer you
there. Thank you guys so much for
watching and I will see you in the comments. Bye!
[music only]
-------------------------------------------
Tyron Hapi ft Bianca | On The Run | Drum Cover | Tone Cola | Drum and Dance Videos - Duration: 3:56.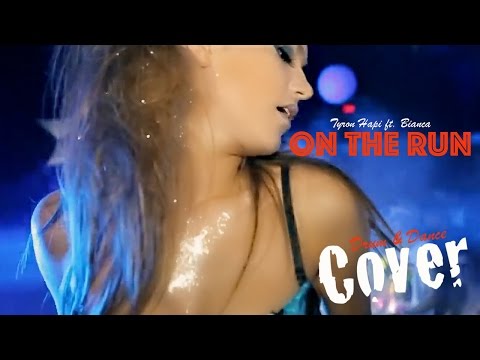
-------------------------------------------
GILGAMESH [1/6] : Gilgamesh & Enkidu, chants 1 & 2 - L'ARCHE - Duration: 20:09.
-------------------------------------------
Model Finishes & Painting Techniques | Video Workbench - Duration: 54:40.
welcome to the video workbench classic series instructional video
model finishes and painting techniques
what's the first thing you see when you look at the model finish now creating
attractive attention model finishes is easier than ever and as a special bonus
you get complete airbrush instructions from an airbrush compressor and applying
paint radio model cars armor or aircraft this video is packed with must have
detail every modeler needs
originally produced in 1992 the techniques using this deal still cover
everything you need to get going with your model kit the examples shown here
really haven't changed too much there is no definitive way of building a model
kit everyone has their own way of doing things and with time so will you
this video teaches dozens of useful tips no matter what your skill level
including what I consider that three important keys of model kit building
tips tools and techniques I would like to talk a little bit about the
instructor in this video is a former United States Air Force guy here who
made extensive use of his models and photography during his military career
he has used his mouth photos for intelligence briefings and often fool
experienced officers as market photographs have appeared in trade
magazines such as the journal the International plastic model of society
and finds you modeler just to name a few
i hope i watching this video that you walk away with a better knowledge of how
to safely and correctly assemble a plastic model kit along with happy found
or coming back into a hobby that is very fun and rewarding thank you and enjoy
hello and welcome to video work bench model finishes and painting techniques
I'm your host Chuck Davenport my boy and I are here building one of these
marvelous little snap take its course at his age but the most he's able to do is
put the wheels together and apply these cells stick decals but you're probably
at the point where quality and accuracy of you finish are very important and if
that's the case my boy and I have a video for you ok what's next year we
have to put the wheels on here listen to him snap 123
to demonstrate techniques of the TV award-winning finishes will cover
surface detailing weathering and applying decals much of the finished
work I do is accomplished with an airbrush so let's cover that topic first
for most of my painting I'll be using Tosh brand airbrushes this is a simple
external mix single-action device which allows you to control only the air flow
with this push button volume is controlled with a variable nozzle
interchangeable tips give you more flexibility in the size of the spray
pattern this external mixed double action posh airbrush allows you to
control booth air flow and volume with one button check with your local hobby
shop there are a number of different brands available ranging from 10 to $15
all the way up into the hundreds airbrush is a very delicate instruments
and require special care keep viewers spotlessly clean even minut amounts of
pigment can clog your airbrush and drive you to distraction I clean mine with
lacquer thinner disassembling the brush and cleaning the parts with pipe
cleaners as an option you can store your tips and thinner
industrial such as ek to clean your brush if your brushes rubber seals it
soon won't after Nek gets to them in the heat of battle you may not have the time
to disassemble the airbrush in this case you can get away with sprained solvent
through the tip and cleaning the cup make sure you go from light to dark
colors to minimize the effects of pigment contamination and don't do this
too much plan your work and make time to clean the tool properly there are a
number of air sources available such as cans of compressed air available at your
local hobby shop or Walmart compressors like this old when I use cost about $100
if you're in the hobby for the duration I would encourage purchasing a
compressor a simple holding tank made from a propane bottle helps to smooth
out the airflow a water trap is absolutely essential water mixed in with
pigment will ruin finish this particular device incorporates a pressure regulator
and was purchased at a national hardware chain store for under $40 I live in
Georgia where humidity is a real problem so I also have an inline water trap
airbrush is a very versatile tool and will accept a wide range of paints
including acrylics lacquer and enamel the new acrylic or water-based paints
are environmentally friendly but you have to be very careful about mixing and
surface preparation lacquer based paint dry quickly but can attack plastic if
used improperly and animals are the easiest to work with but because of
their long working time you really have to be concerned with protecting the
finish from tests while driving rather than trying to explain the benefits or
drawbacks of a specific brand I will explain my preferences as I go along the
final choice of course is yours
the key to an award-winning finish its surface preparation
the surface must be perfectly smooth free of pits scratches or surface
blemishes I went polish the surface with 600 grit sandpaper after working out
scratches with course regrets you can check the fidelity of your work with a
light coat of gray or aluminum primer the paint reveals any flaws these can be
filled with putty your favorite brand likely contains toluene which allows the
body to bond with the primer so you don't have to remove paint in order to
add more party once you're satisfied with the service you can move on
preparing our model for painting by masking off appropriate areas artists
risk it is great for demarcation lines but inadequate for compound curves
masking tape can be cut to adhere to curves but you must burnish the edge to
keep paint from seeping under canopies can be masked with Scotch tape scored
the table a sharp knife and remove tape from canopy frames so that these can be
painted if you are building an airplane windows in the fuselage can be filled
with a thin mixture of white blue water and a couple drops of dishwashing liquid
after this dries it acts as a mask my absolute favorite primer is flow cool
grey primer available in their railroad range of colors mixed the primary with
lacquer thinner 60% gray and 40% thinner you can use measuring cups or eye
droppers just keep the basic mix consistent for almost all airbrush work
I do I start with this basic mix and then I strain the paint into the cup to
remove clumps of pigment and other impurities oh by the way the strainer is
really high tech sections of old pantyhose test your basic mix
each paint has unique characteristics try to use fresh paint to minimize the
effects of aging on the pigment such a compressor at about 40 pounds of
pressure and test the spray if it comes out in clumps or spatters it's too thick
add a drop of thinner if it's praising streaks it's too thin at a drop of paint
keep testing to the point where you get a smooth even spray there is a direct
relationship between air pressure and pain viscosity at forty pounds of
pressure the basic 6040 mix is a good starting point however if your air
source puts out less pressure you will need to thin the paint even further for
the purposes of the video my mixes and pressures are based on the use of a
compressor with a regulator mount your model or parts with toothpicks downs
bent wire anything to allow you to pay the peace without handling it is
handling is a must do so with disposable gloves available at pharmacies the model
must be free of oil and grease so I give it a rub down with a clean white towel
moistened with mineral spirits or paint thinner just prior to every painting or
clear coat I wipe the part lightly with the tack rag to remove last traces of
dust I like local grey primer so well because it bans permanently to plastic
by attacking a chemically to keep from crazy and distorting the smooth surface
of the plastic missed on several barrier coats after you lightly covered the
model you can come back with one or two wet coats remember to spray at an angle
to help spray away any unseen dust particles if you use a thick primary
such as that from a spray kin you may need to gently scribe panel lines to
restore detail covered by the primer if you use for local great primer the paint
will dry quickly enough so that you can complete the process in one session
however let the primer dry for a day then go back and check for any further
flaws or imperfections these must be sent it out and then we primed just can
be a time-consuming and largely boring process but for any model in any scale
it's an absolute necessity to get an award winning finish what's the part
with 1000 grit sandpaper a light touch is called for
especially around the edges the idea is to obtaining a smooth finish on the
primer try the model periodically and check for rough spots don't hurry
remember you get out what you put in
remember that the bane of the model painter is airborne dust and chemical
odors if you don't have an elaborate spray and dust removal system a simple
cardboard box and a three-stage air cleaners such as this one from VA
environmental marketing will do the trick
the 18 scale Tamiya by motor motorcycle I'll demonstrate techniques that I learn
from master modeler and friend Pat covert from Birmingham Alabama on how to
achieve unbelievable gloss finishes from either a spray can or an airbrush if
you're in automotive modeler this is the finish for you I'll be using tackle
gloss white enamel in a basic 6040 mix and forty pounds of pressure technique
start and finish brain outside the park hold your airbrush about 6 to 10 inches
from the part and adjust the novel can deliver a fine mist mist on several
light coats allowing the paint to dry for 20 minutes in a dust-free area don't
try to cover the primary and one code used at least three missed cuts spray
undersized and other parts the same color you use the same techniques with
spray cans except that an animal paint out of a can seems to spray better when
it's warm so the candid about three inches of hot water for five minutes
also hold the can tend to 12 inches from the surface to be sprayed since you
can't control the flow of paint as well as an airbrush paint parts with compound
curves one section at a time taking pains to keep the coverages even as
possible the hard part that requires practice and patience is applying the
wet coats the idea is to achieve a deep gloss finish too little paint results in
orange peel and too much results in runs keep a strong light off to the side to
check for gloss if you're using an airbrush
you want to open the nozzle to increase the paintball you you several passes to
build an even gloss and check your work to ensure you achieve an even plus the
biggest mistake people make is not allowing enough time between coats let
you paint set up in a dust-free environment for 30 to 45 minutes in
order to achieve that super gloss finish you're going to have to apply up to four
wet coats follow your last gloss coat immediately with clear gloss let this
setup for 40 minutes then follow with two more clear gloss coat allowing
forty-minute setup times between coats after the last clear code let the paint
cure and a dust-free environment for ten days
yes that's right 10 days work on sub-assemblies
another model go mow the lawn just leave that paint alone for ten days so that it
can cure properly
can be found at Auto Supply stores when all is just one of a number of polishes
you can use on your model check with your local hobby dealer for more
suggestions if you finished up with a slick paint job you can start with a
four or six thousand grit if you have a rougher surface or one with slight
ripples start with 2402 3600 grit sand dry so that you can monitor the progress
of your work
wrap the measure around the block provided in the kid and start sandy use
a light touch and sand in strokes not circles the first grits will dull your
finish greatly don't be alarmed you will notice the course grits taken the
ripples out of the paint leaving the glossy low spots continue sandy until
the surface is uniformly dull gradually work your way up to 12,000 grit at which
point you will be amazed at the quality of your finish apply a tiny dot of went
off to a warm rag and polish I stay away from cotton because the weave acts more
like sandpaper I prefer went off because it polishes and waxes at the same time
if you use straight polish you will want to finish the job with a fine quality
wax such as the treatment detail wax available at hobby shops if you intend
to add water transfer decals you need to stop just prior to adding additional
clear coats remember that decals must always be applied to a glossy surface
regardless of whether it's a car a tank and they're playing or whatever to apply
water transfer decals you need a pair of scissors tweezers a soft brush a dish of
clean warm water and a decal setting solution
your decals out a gesture model so that the service you want to work is
accessible dip your dick Alen warm water for about 10 seconds
remove it and let the water drain on a towel for about another 10 seconds
test the decal it should slide easily if not dip it once more for another 10
seconds
moisten the parts lightly with water slide decal off and position it with a
brush you may need to hold small decals with tweezers carefully blot excess
water away with the town taking care not to move the decal it never fails use a
moistened brush to smooth out bubbles and wrinkles now let the decal set for
about 10 minutes you can move on to other decals decal setting solution
allows the decals to adhere closely to the surface and any surface detail test
a scrap piece before using the solution apply the solution with brush to the
entire decal surface don't be alarmed what happens to the decal and don't try
to touch your position and you will ruin it just let it dry for a day if as in
the case of the ten-year Bimota motorcycle you have decals that made to
former Finnish make sure you overlap them about one millimeter to account for
shrinkage this will give a smooth unbroken finish lets the decals of dried
you can resume with a glass overcoat sanding and polishing treatment that I
described earlier resume with the glass overcoat sanding and polishing treatment
you'll be amazed at the depth of the finish and the Glasgow will completely
hide the clear decal film this technique for achieving super gloss finishes
requires patience and attention to detail but the results are well worth it
in a contest the first thing the judges notices to finish you can have loads of
scratch built detail in the model but that doesn't necessarily guarantee a
winner
a model executed cleanly and simply with us stand out finish will be the winner
let me assure you that these painting techniques work equally well for
automotive lacquers fingernail polish acrylics or just about anything else
that can be put on plastic or metal a word of warning though don't mix acrylic
paint with enamel or lacquer paint you can spray acrylic over enamel or lacquer
primer be very careful spraying lacquer over an animal it can damage the paint
but an animal goes over lacquer quite well I highly recommend testing your
paints on pieces of scrap before you work on the model
let's talk about making your own decals often you will need decals were none are
available I needed some cock pit nomenclature for this P forty cockpit
it's as simple as buying a sheet of clear decal film from your local hobby
shop and creating the artwork on a typewriter or desktop computer with a
laser printer reduce your artwork to the size needed on a reducing copy R Us
section of clear decal on the correct side and position of the sheet of paper
that will be run through the copier
you now have a reduced copy of your artwork on clear decal still put a coat
of clear lacquer or enamel on top of the decal and let it dry the beauty of this
technique is that for a few dollars and the color copier you can create or
reproduce virtually any color artwork and make it into a decal are things to
IP most director local chapters Bruce rate above for this useful tips
especially combat aircraft you need to decide up-front whether the aircraft
will appear as it did when it rolled out of the factory or at some time during
field service wartime and field service subjects the aircraft to various degrees
of wear and tear also do your homework to determine the correct colors for your
camouflage scheme museums books magazines shows and other modelers such
as those night PMS are valuable sources for this type of information I often add
bare metal four panels to various parts of the aircraft this helps to add some
diversity to the otherwise uniformed services of a model cut a piece slightly
oversized and burnished with a q-tip or a dry transfer burn assure available at
art supply stores on compound curves apply the foil to the high side of the
curve and work outwards finally cut and trim the excess
finished begins with proper surface preparation and priming washed the parts
sand the part smooth apply your primer and the primary smooth to get added
depth to the camouflage game highlight panel lines with flat black using a 64
remix forty pounds of pressure and a fine spray a three-by-five card access a
mask using the color scheme from the Ministry of small aircraft production
decal she values Humbrol paint to cover the sides and undersides light blue once
again begin with the basics 6040 mix and forty pounds of pressure don't try to
cover and one coat spray three light coats to get basic coverage then add
paint where necessary to blend the black panel detailing in begin masking for the
final camouflage colors I'll use masking tape to mask the leading edges of flying
services trailing edges are covered with artists risk it to prevent overspray
cover the remaining areas with tape and paper on this aircraft the lines between
different colors with soft which is to say darker colors were lightly feathered
at the edges where they met lighter colors to achieve this effect the mask
line needs to lie slightly above the surface of the model to help simulate
the uneven edge I tore a piece of card and taped it in place
spray your first camouflage color 60 40 minutes forty pounds of pressure I'm
using home rose brown violet build the color using a fine spray you should
still see the very faint outline of the black panel lines I'm partial to humble
because of its fine pigment but I have to give a plug the guns he saying you
and their superlative aqueous color range using cards cut to size hold each
one in place and spray up to the card use a fine spray 60 40 minutes
forty pounds of pressure and build the final coat with the intention of finally
feather in the edges in this case the color is homegirls dark green in order
to achieve the modeling so characteristic of Luftwaffe aircraft
will change the mixture ratio and pressure settings once again the ability
to regulate air pressure will prove very helpful in creating different effects
and there are at least three methods of appliance soft model camouflage one
involves making elaborate masks and the other requires delicate brushwork and
oils by far the easiest is airbrushing using a 40 60 mix meaning 40% pigment to
60 percent thinner 15 pounds of pressure and a fine spray test the pattern on a
piece of card before committing yourself to the model once satisfied with your
tests spray small irregular patterns of brown violet then switch colors and do
the same for dark green the spray should be so fine that you have to build color
finish off other color details such as writer and spinner then let the pain
cure for a couple of days
inspect the finish for any flaws and correct these with a light sanding and
restrain white the tack rag and give a good coat of clear gloss testers glass
code works well apply decals as described earlier
keep in mind that during field use many factory stencil markings were
obliterated after frequently paintings and touch-ups once complete protect the
decals with a code of testers dull coat
now the real work begins whether in an aircraft is a slow process that demands
attention to detail and certain fitness overdone it can look very bad but
applied with subtlety and restraint weathering can be most effective in
telling the story of an individual machine this detail to execute his panel
detail simply use a number to mechanical pencil very sharp to pencil in panel
detail I have seen ink used but I don't care for the technique too much it's not
very subtle
spray the area behind the exhaust stack will define miss the flat black build
the painter so that the black aids in two aircraft color the further back you
go
dark grey pastel powder
the wing walk and cockpit rail frequently had paint worn off to achieve
this effect use a section of soft cloth wrapped around a Q-tip tip this in
artists metallic powder aluminum here
rub this aluminum out on a scrap service still nothing but a dull black smudge
remains on the clock now dry brush the walkway and rail until the desired
effect is achieved often leading edge paint was worn away due to the action of
airflow combined with dirt and dust sort of a sand blasting effect this too can
be simulated with aluminum dust paint frequently chipped off and other areas
too so dry brush flat aluminum on selected areas of the leading edges of
flying services spenders panels and cockpit frames you can also scrape small
bits of pain away from the areas covered with bare metal foil remember don't
overdo it even with larger subjects field conditions were not conducive to
clean aircraft light-colored services would get dingy quickly use earthtone
pastel powders to remove the fresh paint look from the aircraft hinge joints
around runners elevators and ailerons can be given an appearance of depth with
a bit more pastel powder
will prevent the paint underneath from being weathered in this case mix some
paint color with pastel chalk and dry brush the clear decal film a steady hand
is needed
build the effect gradually no matter if you get paint on the decal in many cases
national markets were painted on the aircraft and suffered the same effects
of weather and don't forget wheels since ww2 aircraft often operated off of grass
field you can use earth tone pigments to build up layers of mud or you can mix
passed up powders with a dab of white glue and with water
favorite technique of contests caliber modelers is to use a toothbrush to spray
earthtone pigments on the undersides that might normally be spread by wheels
in actual service check your sources aircraft leaked oil the airstream causes
it to streak along the fuselage a small dot of artists Inc from a repeal graph
Penn Street with your finger does a nice job of simulating those oil streaks
there are many other details you can add to your model it's a matter of taste
time and money a word of caution though many of these weathering effects of
perishable so protect your model from dust and handle it carefully now let's
move on to another finish that gives modelers fits natural medal
finishes remove all raised panel lines with 400 grit sandpaper polish with 600
grit prior to spring white but a Craig put a thin coat of clear gloss varnish
using a 60 40 mix on your model any garden variety will do as long as it's
not polyurethane let it dry overnight in a dust-free environment the next day
inspect and remove any flaws wiped the tack rag spray another coat of varnish
and let it set up in a Destry environment for two hours depending on
atmospheric conditions the varnish should be virtually dry to the touch
actually it's a good idea to spray a scrap piece of plastic to use as a test
article when you touch the surface you should feel a slight tackiness but no
residue should stick to your finger you know like a post-it note chippewa we're
going to artists aluminum powder and begin buffing the varnish no need to
skimp on the powder you should see a glossy almost chrome like surface
developing a few Buffalo varnishes to dry the finish will be glossy but
transparent if you before it's too wet to finish will be dull after the finish
is cured white the model with attack Craig which will realistically dull
finish and recode with varnish repeat this process to produce a finish that
will resist damage from any subsequent masking once cured the finish is ready
for detailing and some diversity to the overall aluminum finish with the
following techniques bare metal foil panels rotate the grain for a different
effect
aluminized finishes such as humble silver or local gold silver painted on
clear decal film masking selected panels with artists risk it and repeating the
vanishing procedure but this time adding black copier toner to the aluminum
powder to change the shape of aluminum outline bulkheads ribs and rivets with
an artist stump dipped in powder this traded is a discarded vacuum cleaner
belt with a piece of felt attached this keeps from our in the surface
you can easily put a metal finish on any complex surface the wheels on my Bimota
are done and gold powder I wanted something really different yet
convincing from my 143rd scale 57 Chevy in fact I even treated the photo etched
sheet so that my grill and wheel spokes had a gold tone finish I was rummaging
through my models and found a conceptual kid at the B two bomber by model
technologies this was back before anyone had an inkling of what the be to really
look like the kids basic Delta shape look nothing like a bee to but could get
some styrofoam and bondo be made to look like Aurora the alleged super-secret
replacement to the sr-71 the problem but all those models of u2's sr-71 stealth
fighters is the monotony of a black finish I didn't want my Aurora looking
like a huge black blob so here's how I added some variety to the basic black
finish on the Aurora described penalize using various templates since I have no
references my panel lines are based on what I think the aircraft may look like
and my knowledge of how airplanes go together after cleaning the surface of
any oil residue in plastic bits I primed and sanded as described earlier I'm
going to put down a code of packed red dark grey the actual hugh was not so
important
some I prefer like Ghost Grey but I wanted to keep all the colors tone down
once finished the great will simulate walkway markings and sensors for this
reason I will completely cover the top but only selected sections of the
underside using one-sixteenth inch wide Chartpak tape lay out the walkway lines
I am basing the walkway pattern on photographs of the B two stealth bomber
as a reconnaissance platform the Euro would need electronic sensors that would
not compromise the aircraft stuffiness
to simulate these sensors I will use sections of wedding veil material
available at any fabric shop these are cut slightly larger than the panel later
material and police taking care not to distort it
will also be equipped with optical sensors so I dropped out some 18 inch
diameter holes there's no master plan here on the size of the hole the size
and location just looked right I imagine that the Aurora would have an attitude
control system much like the reaction control system used on the space shuttle
to simulate these I cut bare metal foil to size again I'm just guesstimating
here next day used a metal punch to score holes in the fall peace after
carefully lifting the rectangular piece and leaving the foil circles behind I
rub the foil rectangle in place after masking cockpit windows I sprayed the
aircraft in overall flat black using testers paint job of adding diversity
and interest to a rather dull paint scheme involves generating a variety of
hues of black remember that the eye is disturbed by asymmetric patterns so if
you have a particular shade on one side of a model balance the model by applying
the same shade to the other side if you need to decrease the tackiness of the
tape
your forehead this color is flat black mixed with purple in a three-to-one
ratio of black to purple your TV might not show these subtle shade but in
person they're quite evident if you get a piece of dust on your freshly painted
surface use a piece of tape to pick it out and then respray use royal blue in
the same proportions to get a slightly different shade stay away from the other
colors unless you need a really strange shade you can add white but you're
really just making shades of grey this shade was created by mixing three parts
gloss black 21 parts over after it dried for a day I rub the finish out with that
same piece of material I used earlier to simulate aluminum showing through the
war in camouflage of the BAF 109 you want to use this affects sparingly
because it really stands out by mixing glass black and silver fifty-fifty I got
this standout engine color on the by Moda after I rubbed it out to simulate
what I envisioned to be absorbing leading edges I needed an absolute dead
on flat black the aircraft was mask and sprayed with a garden variety of Mac
varnish using the same technique for creating a metallic finish I rubbed
copier toner onto the varnish the effect was so striking I used the same on these
heat vent louvers and some other areas
an important aspect of modeling subjects that may not actually exist is
visualizing what they should look like Hollywood production designers do this
when they create vehicles and spaceships for science fiction films with the
Aurora I envisioned a vehicle operating in the upper fringes of the atmosphere
on a slush hydrogen propulsion system since extreme heating create an ionized
layer of gas that shows up on radar my Aurora would need a system to capture
and dissipate as much of the heat as possible so the leading edge captures
heat which in turn is used to warm the slush hydrogen to operating temperatures
what little heat remains is vented upward into space where it would be
undetected by radar this visualization dictated my design panel line placement
and color scheme
for yet more shades of black I cut a mask from a three-by-five card to
simulate a small access panel and artists charcoal on the area
graphite color works well also and leaves an interesting is she
to add further contrast between different panel highlighted panel lines
with a number to mechanical pencil
finally I cut a few other masks from three-by-five card and spray different
areas with a clear semi matt lacquer to vary the tone of the basic black black
the result after only a few hours of effort is the completed Aurora it has a
basic yet varied black finish
issued a challenge in the journal of the International plastic model of society
the challenge was to build a post nuclear war era concept vehicle I came
up with a vehicle that resembled a tank from a commuter's worst nightmare I
built this vehicle to demonstrate some modeling techniques that will work on
any armor model other than cleaning mold release with mineral spirits know
whether painting preparation was done next I added damage to the vehicle by
grinding plastic away with a dremel tool
one other technique is to distressed the plastic used in a soldering iron I
prefer the soldering iron to direct flame because I can control the effect I
use a 15 watt soldering iron
the forward gun turret cobble together with parts from the scrap box was
distressed the same way the main gun turret was a simple box constructed from
sheet styrene I wanted to depict welded steel suffering the effects of weather
in combat to simulate a weld joint glue a piece of stretched sprue into place
the diameter of the sprue is dependent on the size of the weld joint and scale
using this precise mathematical formulation guessed that a diameter of
about one millimeter would do just fine using the soldering iron I gently push
the tip into the sprue creating a fair representation of a weld joint this
technique was carried through to the scratch built tank chassis
the blast damage was created by gouging the sheet plastic with a dremel tool
then the soldering iron was used to detail the effect finally I used a 240
grit sandpaper to take some of the rough edges off and make the blast more
homogeneous you see anti armor weapons used the extreme heat resulting from
terrific pressures to melt through armor the blast effect is largely coincidental
the car body was primed with local grey primer and sprayed with a code of packed
reflect red absolutely no attempt was made to lay down a pretty finish I
wanted grunge however I was mindful of dust the gun turrets and steel plate
armor were primed with actress steel and left that way to simulate arrested
finish I dusted local rust over the entire model until I had laid down
enough pigment to satisfy my tastes a little damage done to the flat red in
steel would be a welcome benefit to the overall grand genus of the model no
mercy for the chassis this was paid it overall rest when you spray a wet coat
of lacquer on styrene it usually crazy as the surface which in this case was
just fine
severely rusted and pitted areas such as fenders and punctures were created by
applying a thin coat of superglue before the model was primed then sprinkle
baking soda
yes that's right baking soda over the glue the to form a chemical bond that is
very strong in fact this makes it great gap filler but it's very difficult to
sand after the painting is done
go back and brush this area with local rust and feather the rest into the
surrounding paint using a dry brushing technique once dry seal with clear flat
next give the area a washer flat black finally burnish the high spots with
burnt sienna pastel chalk
keep in mind that this last step is highly perishable so this should be the
final details step just before the model is set up for display you can also use
the rest of our system to addressed to previously painted parts railroad
modeling shops generally carry this product but you can ask your local hobby
dealer to order it for you with basic construction surface detailing and
painting complete and a day for the paint to cure it was time to seal the
finish with a protective coat of clear matte test result code works well for
this and provides a good base from which to begin detailing Romanian areas such
as the steel plate corners and blast damaged or dry brush with local rust to
add visual drama to the high and low areas the model was given a light washer
flat black
ground vehicles quickly show signs of accumulated dirt if not cleaned
regularly and my post new vehicle is no exception to dramatize the effects of
Sun and dust I missed it on a coat off local grey primer over my completed work
I used a seventy thirty mix of lacquer thinner to pigment at forty pounds of
pressure and a fine spray at a distance of about two feet from the model the
airbrush deposits and almost imperceptible layer of gray pigment only
spray for about 10 seconds that's enough you really don't want to see the pigment
but its presence on the model reflects light and influences the eye of the
viewer money up the vehicle using a toothbrush and earth tone pigments I
rushed to the road wheels and muddy them with rust off this is great stuff it
looks clumpy and messy like dried murdered you simply apply a coat of thin
white blue and then sprinkle on the mud and grungy road wheel
with matt lacquer and apply a black wash if you want to add a deeper level of
grunge when you detail chrome parts it's best to remove the chrome you can do
this by wrapping a piece of cloth around the shank provided in a dremel tool kit
the spinning radware away the chrome leaving their plastic underneath once
you've completed simply you may need to go back and spruce up the past 20
shading you did I like to rub some earth tones on my finish to add further depth
and enhance the effect started by Miss Teen flow cool grey remember thats
affects the top and murder affects the bottom in between is a mixture of the
two
the coup de Gras of any ground vehicle is fuel and lubricants stands there are
a number of techniques for simulating the effect my favorite is for local
grind this is clump Eaton St look and stuff
loader brush with lacquer thinner dip it into the local crime and then read it in
the thinner drain some excess onto Atal then apply the stain to the surface and
let it run down the side repeat as necessary to get the effect you desire
it's better to under do the effect then to over do it because it's easier to
build the effect that it is to try to undo a botched attempt
remember that oil stains will travel for example across the scene and pool and
recessed areas so treat these areas accordingly
pressure oil stains can be made by using glass black and pink dinner if you use
for local rest instead of grime you can achieve the similar effect of dripping
rust stains on water-borne vehicles
this brings me to the close of another video look for other titles in our video
workbench series i'm Jack Davenport and we'll see you next time
-------------------------------------------
Indian party wear dresses for girls Flipkart amazon shopping online 788 - Duration: 0:39.
Indian party wear dresses for girls Flipkart amazon shopping online
-------------------------------------------
Learn Colors With Pink Spidergirl Learn Colors with Candies Learn Colors With Flowers - Duration: 18:28.
Green color
Blue Color
Orange Color
Pink color
Yellow Color
-------------------------------------------
PRESENCE ET ATTENTION: 2 METHODES SIMPLES POUR Y PARVENIR - Duration: 9:26.
-------------------------------------------
Beyerland 390 D SPRINTER - Duration: 1:07.
-------------------------------------------
Outcast 2x04 Promo "The One I'd Be Waiting For" (SUB ITA) - Duration: 0:31.
-------------------------------------------
GILGAMESH [1/6] : Gilgamesh & Enkidu, chants 1 & 2 - L'ARCHE - Duration: 20:09.
-------------------------------------------
THIS IS COMPLETE PI ** EC | OutLast 2 - Duration: 9:29.
-------------------------------------------
PRESENCE ET ATTENTION: 2 METHODES SIMPLES POUR Y PARVENIR - Duration: 9:26.
-------------------------------------------
OMG comment aller sur un serveur privé Clash Royal . Ça marche! - Duration: 1:51.
-------------------------------------------
[CE QU'IL SE PASSE SUR TERRE] 2/3 LE PROBLEME 5/7-1 symbolisme franc-maçon (stfr) - Duration: 26:14.
-------------------------------------------
Haircut in India | Indian Barber hair cut, beard shave and head massage in Kolkata - Duration: 3:15.
So today is our last day in India.
We're here in Kolkata (কলকাতা) in India and it is our very last day.
Tomorrow we're all taking off.
And you know what?
We're kind of looking a little bit scruffy.
Even you.
Not as bad as me.
But we need a shave and we need a haircut so we're going to go and do that right now
here in Calcutta (কলকাতা).
Yeah, I'm looking forward to it.
Clean shaven and a haircut.
All ready back for Canada.
So I had been looking for a place to get a hair cut and a shave on Sudder Street which
is where we're staying and no cigar.
I looked around for quite a while and couldn't find anything but down this street here I
think it is called yeah Hertford Lane I found a little spot and I asked them 'hey can we
go get a shave and haircut' and he said 'yeah of course' and can we film and he said yeah
of course.
So we're going there right now.
A little bit off of the top.
Oh, someone is getting ready for a hair cut.
Are you all ready?
Oh yeah.
Already for this?
Haha.
That is awesome.
Yeah, here we go.
How are you enjoying that?
Yeah, it is great.
Does it feel good?
This is not going to make me smarter.
Haha.
That is good.
Yeah.
We've been taking a lot of train rides and like our you know our neck muscles our back
muscles.
There is a lot of tension.
So this will relieve all of that tension for sure.
Thank you.
Alright, so we've had our haircuts, we're clean shaven and we each got a massage.
And that came to like 240 Rupees.
Which is what?
Like 3 or 4 US dollars total.
So we gave the guy a really good tip.
We gave him an extra over 150 Rupees because the guy did such a good job.
And what do you think of your haircut?
Well it was awesome and the head massage and the upper body massage was well worth it and
you know you just think of the value in Canadian dollars.
Like you just can't.
It is insane value.
But this guy.
This guy is a really skilled practitioner and it is perfect because we're both taking
flights back home from Canada.
.We definitely needed that massage and now we look all clean cut so hopefully immigration
lets us in.
We won't have any problems in immigration for sure.
I hope not.
We're too clean cut looking.
There you go.
-------------------------------------------
(ENG)All Road Shop! Date Make up 💓 K-Beauty l Ella Ahn - Duration: 3:05.
Hi everyone. This is Ella Ahn!
Today Im gonna do "Date" makeup which is really pinkyyyy..:)
I already put some base make up on before the video starts. So its gonna be really short one.
So please feel free to take a look :)
-------------------------------------------
Learn Colors With Pink Spidergirl Learn Colors with Candies Learn Colors With Flowers - Duration: 18:28.
Green color
Blue Color
Orange Color
Pink color
Yellow Color
-------------------------------------------
Indian party wear dresses for girls Flipkart amazon shopping online 788 - Duration: 0:39.
Indian party wear dresses for girls Flipkart amazon shopping online
No comments:
Post a Comment