♪ เวลากู spit เหมือนกูเป็น สัตว์ประหลาด ♪
♪ อุนตร้าแมนขนานนามกูตัวฉกาด ♪
♪ คำกูลื่นไหลเหมือนเป็นสักกะหลาด ♪
♪ หนึ่งในสิบ galaxy กูคือ อุกกาบาต ♪
♪ จดลงบนกระดาษให้มึงเสพเป็นกระจาด ♪
♪ ไม่ใช่เพลงตลาด แต่คำกูยังบาด ♪
♪ เหมือนมีดที่พึ่งปาด แค่เฉือนขาด ♪
♪ ออกจากปากผ่านสมองกูฉลาด ♪
♪ คมยันลูกและติด top นักปราชญ์ ♪
♪ so fresh เหมือนกับผ้าที่พึ่งบิดหมาดๆ ♪
♪ ไม่ต้องวัดของกูกันที่ขนาด ♪
♪ เราต่างกันเพราะมึงแค่ตัวขยาด ♪
♪ คนละ grade ราคา เพราะมึงแค่ผักกาด ♪
♪ กูเหมือนบอระเพชร ที่แม่งโครตจะฝาด ♪
♪ อย่าสบถถ้ามึงฟังตัวมึงเองแล้วกระดาก ♪
♪ วิญญาณเหมือนหลุดภพเพราะโดนกูฉุดกระฉาก ♪
♪ เวลากู spit ทำวิตกจริต ♪
♪ นึกภาพตอนนอนให้มึงหลับตาคิด ♪
♪ เรื่องจริงที่เอามาพูดกูไม่ดัดจริต ♪
♪ โครตreal shit ไม่มีปรสิต ♪
♪ ตอนนี้ไม่ว่างวะ กำลังfuck y'all bitch ♪
♪ bottle on the table sip กันเป็นลิตร ♪
♪ cause we don't do แล้วใครจะ do for this ♪
♪ don't flow don't flip but we all star shit ♪
♪ ah! We all star $hit ♪
♪ ah! We all star $hit ♪
♪ ah! We all star $hit ♪
♪ ah! We all star $hit ♪
♪ I'm a $uperstar $hit ♪
♪ I'm a $uperstar $hit ♪
♪ I'm a $uperstar $hit ♪
♪ I'm a $uperstar $hit ♪
♪ I'm a $uperstar $hit ♪
♪ I'm a $uperstar $hit ♪
♪ I'm a $uperstar $hit ♪
♪ I'm a $uperstar ♪
♪ กูยกระดับ ยิ่งกว่าtroll way ♪
♪ ไม่มีเลี้ยวกลับเหมือนอย่างu turn ♪
♪ ไม่ใช่turnกู แต่กูlearnอยู่ ♪
♪ ไม่มีครูalways do เดี๋ยวกูทำให้ดู เดี๋ยวพวกมึงก็รู้ ♪
♪ am ma dirty man แถมยังPSYCHO ♪
♪ fuck the popo. fuck what chu told ♪
♪ when it's time to roll เดี๋ยวกูพาshow ♪
♪ กูยังรอผู้ชมคาดหวังจะมากโข ♪
♪ เปลื่ยนคนโง่จากตัว X กลายเป็นตัว O ♪
♪ ขอโทษทีถ้ากูไวไป but can't stop we need to go ♪
♪ และขอโทษอีกทีถ้าเพลงกูแรงไป ทำมึงk.o ไม่กลับมาo.k ♪
For more infomation >> OK - MON$TER P (Prod.Santos) - Duration: 2:46.-------------------------------------------
Kegerator Build with Fridge Teardown - Duration: 12:32.
[ ♫ Intro Music ♫ ]
[ ♫ Noir by S Strong & Boogie Belgique ♫ ]
Hey, Internet! Today we are going to build a kegerator out of a mini-fridge, with
enough space for two homebrew kegs. We're also going to be tearing this fridge
apart so that you can see exactly where the condenser and evaporator lines are
run... so that you do not accidentally drill into them. The reason I have a
spare fridge to do this is because I accidentally drilled into them.
Moving on!
I'm using Cornelius Ball Lock kegs -- common for homebrewing, but they can differ in
dimensions. These ones that I have are about eight and a half inches in
diameter and just under 25 inches tall. Some of them are shorter and wider, which
makes it a little more difficult to find a fridge where you can fit two side-by-side.
If you have the option, go ahead and go with the thinner ones.
Now, our fridge...
with the shelves removed we have a footprint of sixteen inches by eleven and a half
inches, which is just enough to squeeze the two kegs in side-by-side.
To make sure everything fits comfortably, we're going to need to remove the plastic
molding and a little bit of insulation from the door, and -- vertically -- we need to
bend the freezer tray down to the back to make sure that we have enough height.
So the next step is to take this freezer tray and bend it flush against
the back of the fridge.
Before we bend down the tray, we have to remove the control unit, which is just a single Phillips head screw.
There's also a temperature probe that you'll need to disconnect from the freezer tray.
There's two Phillips head screws on each side that we're going to need to undo before we can bend it back.
And then, once we do, be EXTREMELY careful to make sure you do
NOT puncture the coolant line in the back of the tray.
Now, on this fridge, the freezer tray has a bracket that holds the feed line in place.
I recommend clipping that out (with a pair of clippers) before you bend it down
just to make sure that you don't put any added strain on the line as you bend it.
Put some pressure upwards on the line in the back...
You're going to need to move the control unit up and over the tray.
And once you have it in place, you can go ahead and screw it back in with the two original screws.
Go ahead and find a spot to remount the temperature control unit. On the side
vertically here is a pretty good option, depending on how you want to fit your
kegs and your CO2 tank in there.
And then you're also going to want to make sure that you remount the temperature probe onto the freezer tray
in its original spot.
Once you have the freezer tray bent down to the back, you can go ahead and
test fit your kegs. If they're the same dimensions as mine, you'll see that they
aaalmost fit but not quite. Not enough to close the door all the way.
So, what we're going to do is go ahead and trim down these plastic ridges on the door...
...take out a little bit of insulation, and then we'll have enough room for everything to fit
nice and comfortably.
Before you start modifying the door... on the bottom here
if you undo the screws, you can go ahead and remove the door before you start cutting the insulation.
Set that aside...
Now, with the door, all we really need to do is cut out this
plastic so that it's nice and flat and it doesn't bump into the kegs when we
close the door. The easiest way to do that is either with a box cutter or an exacto knife.
If you follow the seam along the edge you can press the knife right in...
Now you have just a flat door.
Alright, we've got our door back on, we have our magnetic
strip back on... it's a bit of a tight fit with two kegs in there, but the door
closes all the way, which is all we need. If you do want some more tolerance you
can go ahead and trim some of the plastic and insulation out from the
sidewalls which will give you plenty of space.
Another option, which is what I did, is to add a buckle latch to the door.
...to make sure it stays closed and gives you a good seal.
At this point, we are basically one draft tower away from a
kegerator, which means it's time to start thinking about where we want to drill a
hole. So, let's take a look at our sacrificial fridge and see where we can
drill without hitting anything. With the foam removed -- or mostly removed -- you can
see we have the evaporator line in the back and the condenser lines on the
sides, primarily, with a little on the top and the back. The condenser lines are
primarily on the sides of the fridge and zig-zag back and forth about two inches
apart. On the top, the line crosses over and loops out toward the middle about
eight and a quarter inches from the back edge of the fridge, and then zig-zags
again on the other side. The evaporator line comes up from the bottom on the
left, loops once and then connects to the
freezer tray. On the right hand side, we have the wiring for the temperature
control which is clipped here but normally runs up the side to the control
unit. We also have an insert on the right hand side where the switch for the
door sits. For reference, here are some drawings based on the fridge teardown
but again remember that you'll want to leave plenty of clearance when deciding
where drill your holes because this can definitely vary from fridge to fridge.
So, from our sacrificial fridge we know that the condenser line comes out
approximately eight and a quarter inches from the back edge.
It's about two inches wide. The fridge is nineteen and a quarter inches wide so the
center line is nine and five-eighths inches. So, I'm going to drill the hole for the
draft tower ten and a half inches from the back edge. That gives me enough
clearance to drill just under a three inch hole, and also leaves room for the
four mounting holes for the flange. I'm gonna start out with a quarter inch
drill bit to drill a pilot hole, and then use a step drill bit to widen it to an
inch and a half which is enough for two beverage lines. If you want a larger hole
you can use a hole saw, although the step drill bit is really the easiest way to
go on the sheet metal.
[ drilling ]
If you use your pilot hole to mark out the diameter on the inside,
you can cut out the plastic, remove the foam carefully, and convince
yourself that there's no lines that you're gonna hit when you widen the hole.
We look to be in good shape! You can see the sheet metal on top... you can see the
pilot hole, and there's no condenser lines in sight so we can go ahead and
widen this hole with the step bit.
[ hole diameter intensifies ]
[ dremeling ]
Optionally, I put another hole on the back...for gas lines (if you want to keep
your CO2 tank outside), or have a secondary nitrogen tank, or run any wires
in for a BrewPi or anything else. This hole actually doesn't take any drilling
at all. There's already a hole in the sheet metal -- where I assume they spray
the foam in (?) -- so you can just cut through the foam and the plastic and then you
have your secondary entry point.
We've got the holes marked for our flange.
Again, you want to make sure you're at least eight and a half or nine inches from the
back edge to make sure you avoid that condenser line.
[ drilling resumes ]
That is the last of the drilling, and we're ready to mount our tower.
I also 3D printed plastic inserts for the holes that we drilled, just for appearances. One for the top one
for the back, and then corresponding pieces for the inside.
I'm using 1/4-20, two and a half inch hex head bolts with a flat washer on each side.
[ ratcheting ]
This is our final fit with two kegs and a five pound CO2 tank.
The tower that I'm using is a three inch diameter chrome ABS draft tower from Williams Brewing
with two Intertap tower shanks and faucets. The drip tray with the tower cut out
is also from Williams.
Your keg will have an inlet post for the CO2, sometimes
designated by a star-shaped base and the outlet post for the liquid.
The connection to the post is a ball lock quick disconnect -- black for liquid and
white for gas. They are not interchangeable. The way these go on is
to pull up the flange, pop it onto the post, and release the flange.
If your disconnects have hose barbs, you can attach the hoses directly. I prefer to
use the flare nuts.
the tower shanks have a 90 degree hose barb with a curved flange to match the
curvature of the tower, and then an associated curved insert for the inside.
You'll want to start by attaching the hose to the shank with a hose clamp.
3/16" inner diameter is the common size for beer tubing.
On the other end of the tubing, attach your flare nut, but do not attach the quick disconnect
just yet, as we still need to feed this down through the tower.
Make sure you have the flange on the outside, and then start feeding the tubing into the tower.
Before you feed it all the way down into the fridge, add your curved insert and the shank nut.
If you have a shank wrench, you can try and use that to tighten the nut, but...
it's a tight fit in the tower no matter what, so I always end up tightening it with some needle-nose pliers.
Then feed the lines down into the fridge.
We have some insulation to keep the beverage lines cold in the tower.
You can try and squeeze that in through the top, but sometimes it's easier to
just disconnect the tower and put it in through the bottom.
That's all there is to it! I hope this was helpful, and...enjoy your kegerator!
[ draft beer pours ]
Cheers!
[ ♫ Outro Music ♫ ]
[ ♫ Noir by S Strong & Boogie Belgique ♫ ]
© Zemba Craftworks 2017
-------------------------------------------
CLASSIFICA CANZONI OTTOBRE 2017 - Duration: 5:27.
-------------------------------------------
Resultados Loteria Nacional de Panama En Vivo Viernes 29 Septiembre 2017 Gordito Zodiaco Septiembre - Duration: 1:18.
-------------------------------------------
YouTube TV Now Available
-------------------------------------------
Mountain Dew Pop Tarts | How to Make Homemade Pop Tarts - Duration: 5:51.
hey everyone it's James from fun foods and today I'm gonna make these Mountain
Dew pop-tarts now these were simple to do it's a lot of fun
only takes a few ingredients and you're gonna absolutely love them so keep
watching and I'll show you step-by-step how to make these now the first thing
you want to do is start off with this pre-made pie crust now you can get this
at the supermarket now some places you can't get this you would have to make
your own pie crust for that I'm just going the easy route and using this it
says to leave it out for about 15 minutes to get to room temperature so
it's not too cold and I want to cut these into rectangles and I've cut out a
little 3 by 4 inch mold just to use so I can cut this out and I'm going to use a
pizza cutter to cut this and that cuts out two on this side now just take the
scraps join them together and then we're gonna roll these out and cut these to
the same size as that when you have all your pieces cut out just take this set
this aside and now what we're gonna do is move on to our egg wash and I just
have two eggs in here I'm gonna add about a tablespoon of milk you could
also use water if you don't want to use milk and just whisk this up really good
when that's all done we're going to come right back to our cutouts and we're just
gonna brush all in this egg wash I'm gonna do it on all of them some of these
are gonna be the top some of them were going to be the bottom next as our
filling what I'm going to use is this mountain Dew jelly now I made this
mountain Dew jelly a couple of weeks ago I'll put a little card up above as
well as a link to it in the description below go check it out you must see how
to make this jelly it's really simple to do and it's Mountain Dew we're gonna
fill our inside with this Mountain Dew jelly and it should take about a
tablespoon and a half or a teaspoon and a half or so and you don't want to go
all the way to the edges you want to spread it out but you want to leave
about a quarter of a inch fun around the four edges so now what we need to do is
take these and flip these over with the egg wash side down facing the jelly and
we're gonna line them up just like so and once they're lined up we're just
gonna take a fork and we're going to press down the sides this is gonna seal
them
and when they're all sealed up you can either take a toothpick or you can just
use your fork and we just want to pop a few holes in here so that it gives it
some room to blow up and then we're gonna add another layer of egg wash
right on the top here I'm gonna take these put these in the refrigerator just to let
them chill a bit now when your oven has heated up to 425 degrees take these
outer frigerator place them in the oven and we're gonna watch them I'm gonna
think they're gonna cook about 10 to 12 minutes but I'll let you know the end
how long it takes now while that's in the oven cooking what I'm going to do is
make the glaze that goes on top of our pop-tarts I just have a little small
bowl here and I have half a cup of confectionery sugar to that I'm gonna
add about a teaspoon of vanilla extract I'm eyeballing it but you can measure it
out and I'm also gonna add a little bit of Mountain Dew not much be very careful
about a teaspoon mix this up really good
when that's mixed in really good next what we're gonna do is I'm gonna divide
this up so I'm gonna put just a little bit in a small bowl just take some food
coloring not a lot just a little bit of food coloring here or color that green
and the little bowl I'm gonna color yellow
just take these set these aside and we'll use them when our pop-tarts are
out of the oven and when they come out of the oven you
want to let them cool down for at least five minutes even if you're going to eat
them warm because that jelly is gonna be super hot you don't want to burn your
tongue so I'm gonna let these cool down and then we're gonna go on to icing the
top of it so I've let them cool down now and what I want to do is ice the top of
them now that I've given the green icing a chance to cool down and harden up a
bit I'm going to drizzle on some of the yellow icing now I just put it in a
little Ziploc baggie here just to control it you can take your spoon and
just drizzle it that way if you like
here we go all done well now it's time for the taste test I'm going to try one
of these out and I'm taking one that's already been cut in half and let's give
this a shot
good well thanks everyone for watching I hope you enjoy watching you make these
homemade Mountain Dew pop-tarts it was a lot of fun making these and if you
enjoyed this video make sure you hit that like button also hit that big red
subscribe button if you're not already subscribe to get new videos every week
and check out some of the videos I have off to the side I think you may enjoy those as
well and until then I'll see you next time
-------------------------------------------
Jean-Louis Trintignant se confie : "Je pense beaucoup au suicide" - Duration: 2:07.
-------------------------------------------
Pacific Rim Final Battle (Part 1) | Pacific Rim (2013) Movie Clip - Duration: 5:01.
Brace for impact!
Chain sword deployed.
Let's get this son of a bitch!
Gipsy, comin' up on your 12 o'clock!
Full speed!
Get out of the way!
The release is jammed!
We can't deliver the payload, sir!
We're still armed.
But the hull is compromised!
Half our systems are offline, sir.
We need to override the..
Aah!
Both Kaijus converging on striker fast!
Hang on, striker! We're comin' to ya!
No! Gipsy! Do not come to our aid!
Do you copy? Hang on!
Stay as far back as you can!
We can still reach you. We're comin' for you.
No, Raleigh, listen to me.
You know exactly what you have to do!
Gipsy is nuclear!
Take her to the breach!
I hear you, sir.
Headin' for the breach.
Structural damage, 80%. Now..
Mako. Listen.
You can finish this.
I'll always be here for you.
You can always find me in the drift.
We're a walking nuclear reactor.
We can destroy the breach.
What can we do, sir?
We can clear a path!
For the lady!
They're gonna detonate the payload.
He said if you have the shot, you take it!
So let's do this!
It was a pleasure, sir.
Sensei.
Aishitemasu.
-------------------------------------------
Pacific Rim Final Battle (Part 2) | Pacific Rim (2013) Movie Clip - Duration: 5:00.
All systems critical.
Fluid loss.
Systems are critical!
Fuel is leaking!
Our right leg's crippled!
Code red.
Let's finish this. All systems critical.
What are they doing?
Finishing the mission.
Loccent. We have the Kaiju carcass.
We're heading for the breach.
You guys better be right.
'Cause one way or another, we're gettin' this thing done.
On my count, rear jets!
Three, two, one.
Now!
Hold on.
Mako's oxygen is down. Half capacity!
Can you reroute it?
I'm tryin', sir.
Hold on, Mako. Heat shaft purge.
I'm gonna burn this son of a bitch.
They're in.
They're in! It worked.
Oxygen main, left hemisphere, critical levels.
Operating at 15% capacity.
10% capacity.
5% capacity.
He's givin' her his oxygen.
Right hemisphere oxygen..
It's okay now, Mako.
..Critical level.
We did it.
I can finish this alone.
All I have to do is fall.
Anyone can fall.
Raleigh, your oxygen levels are critical now.
You don't have much time.
Start the core meltdown and get out of there.
Do you hear me?
Get out of there now!
One pod is ejected. No detonation, sir.
Loccent, if you can still hear me,
I'm initiating reactor override now.
Manual activation required.
What's goin' on?! Trigger's offline!
He has to do it by hand.
He's out of time.
He has to selfDestruct now.
Manual activation required.
No!
Manual override initiated.
Core meltdown in tMinus 60.
Reactor meltdown in 55 seconds.
50 seconds.
Evac pod engaged.
5, 4, 3, 2, 1.
Reactor meltdown commence.
-------------------------------------------
Racing Sunday /Star Citizen Let's Play /Patch 2.6.3 / ultra wide / GTX 1080 TI / #004 - Duration: 28:47.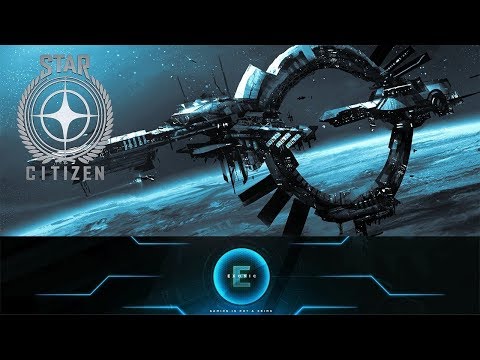
-------------------------------------------
RONALDO FÜR NUR 3K COINS!!! CHEAP ICON RONALDO!! - Duration: 3:46.
bye
-------------------------------------------
Racing Sunday /Star Citizen Let's Play /Patch 2.6.3 / ultra wide / GTX 1080 TI / #004 - Duration: 1:03:57.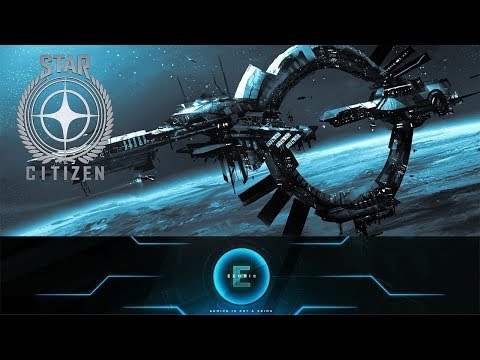
-------------------------------------------
Royal President Hotel in Nay Pyi Taw, Myanmar (Asia). The best of Royal President Hotel - Duration: 5:12.
-------------------------------------------
17 photos incroyables qui montrent que la naissance est la plus belle des choses - France 365 - Duration: 6:30.
-------------------------------------------
VIDEO – Line Renaud plaisante sur le fait qu'elle soit "encore là" - Duration: 2:01.
-------------------------------------------
Audi RS5 - Duration: 1:06.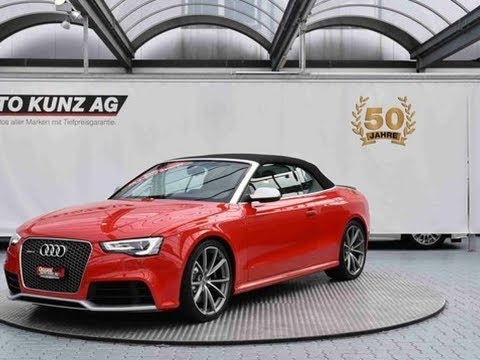
-------------------------------------------
Kegerator Build with Fridge Teardown - Duration: 12:32.
[ ♫ Intro Music ♫ ]
[ ♫ Noir by S Strong & Boogie Belgique ♫ ]
Hey, Internet! Today we are going to build a kegerator out of a mini-fridge, with
enough space for two homebrew kegs. We're also going to be tearing this fridge
apart so that you can see exactly where the condenser and evaporator lines are
run... so that you do not accidentally drill into them. The reason I have a
spare fridge to do this is because I accidentally drilled into them.
Moving on!
I'm using Cornelius Ball Lock kegs -- common for homebrewing, but they can differ in
dimensions. These ones that I have are about eight and a half inches in
diameter and just under 25 inches tall. Some of them are shorter and wider, which
makes it a little more difficult to find a fridge where you can fit two side-by-side.
If you have the option, go ahead and go with the thinner ones.
Now, our fridge...
with the shelves removed we have a footprint of sixteen inches by eleven and a half
inches, which is just enough to squeeze the two kegs in side-by-side.
To make sure everything fits comfortably, we're going to need to remove the plastic
molding and a little bit of insulation from the door, and -- vertically -- we need to
bend the freezer tray down to the back to make sure that we have enough height.
So the next step is to take this freezer tray and bend it flush against
the back of the fridge.
Before we bend down the tray, we have to remove the control unit, which is just a single Phillips head screw.
There's also a temperature probe that you'll need to disconnect from the freezer tray.
There's two Phillips head screws on each side that we're going to need to undo before we can bend it back.
And then, once we do, be EXTREMELY careful to make sure you do
NOT puncture the coolant line in the back of the tray.
Now, on this fridge, the freezer tray has a bracket that holds the feed line in place.
I recommend clipping that out (with a pair of clippers) before you bend it down
just to make sure that you don't put any added strain on the line as you bend it.
Put some pressure upwards on the line in the back...
You're going to need to move the control unit up and over the tray.
And once you have it in place, you can go ahead and screw it back in with the two original screws.
Go ahead and find a spot to remount the temperature control unit. On the side
vertically here is a pretty good option, depending on how you want to fit your
kegs and your CO2 tank in there.
And then you're also going to want to make sure that you remount the temperature probe onto the freezer tray
in its original spot.
Once you have the freezer tray bent down to the back, you can go ahead and
test fit your kegs. If they're the same dimensions as mine, you'll see that they
aaalmost fit but not quite. Not enough to close the door all the way.
So, what we're going to do is go ahead and trim down these plastic ridges on the door...
...take out a little bit of insulation, and then we'll have enough room for everything to fit
nice and comfortably.
Before you start modifying the door... on the bottom here
if you undo the screws, you can go ahead and remove the door before you start cutting the insulation.
Set that aside...
Now, with the door, all we really need to do is cut out this
plastic so that it's nice and flat and it doesn't bump into the kegs when we
close the door. The easiest way to do that is either with a box cutter or an exacto knife.
If you follow the seam along the edge you can press the knife right in...
Now you have just a flat door.
Alright, we've got our door back on, we have our magnetic
strip back on... it's a bit of a tight fit with two kegs in there, but the door
closes all the way, which is all we need. If you do want some more tolerance you
can go ahead and trim some of the plastic and insulation out from the
sidewalls which will give you plenty of space.
Another option, which is what I did, is to add a buckle latch to the door.
...to make sure it stays closed and gives you a good seal.
At this point, we are basically one draft tower away from a
kegerator, which means it's time to start thinking about where we want to drill a
hole. So, let's take a look at our sacrificial fridge and see where we can
drill without hitting anything. With the foam removed -- or mostly removed -- you can
see we have the evaporator line in the back and the condenser lines on the
sides, primarily, with a little on the top and the back. The condenser lines are
primarily on the sides of the fridge and zig-zag back and forth about two inches
apart. On the top, the line crosses over and loops out toward the middle about
eight and a quarter inches from the back edge of the fridge, and then zig-zags
again on the other side. The evaporator line comes up from the bottom on the
left, loops once and then connects to the
freezer tray. On the right hand side, we have the wiring for the temperature
control which is clipped here but normally runs up the side to the control
unit. We also have an insert on the right hand side where the switch for the
door sits. For reference, here are some drawings based on the fridge teardown
but again remember that you'll want to leave plenty of clearance when deciding
where drill your holes because this can definitely vary from fridge to fridge.
So, from our sacrificial fridge we know that the condenser line comes out
approximately eight and a quarter inches from the back edge.
It's about two inches wide. The fridge is nineteen and a quarter inches wide so the
center line is nine and five-eighths inches. So, I'm going to drill the hole for the
draft tower ten and a half inches from the back edge. That gives me enough
clearance to drill just under a three inch hole, and also leaves room for the
four mounting holes for the flange. I'm gonna start out with a quarter inch
drill bit to drill a pilot hole, and then use a step drill bit to widen it to an
inch and a half which is enough for two beverage lines. If you want a larger hole
you can use a hole saw, although the step drill bit is really the easiest way to
go on the sheet metal.
[ drilling ]
If you use your pilot hole to mark out the diameter on the inside,
you can cut out the plastic, remove the foam carefully, and convince
yourself that there's no lines that you're gonna hit when you widen the hole.
We look to be in good shape! You can see the sheet metal on top... you can see the
pilot hole, and there's no condenser lines in sight so we can go ahead and
widen this hole with the step bit.
[ hole diameter intensifies ]
[ dremeling ]
Optionally, I put another hole on the back...for gas lines (if you want to keep
your CO2 tank outside), or have a secondary nitrogen tank, or run any wires
in for a BrewPi or anything else. This hole actually doesn't take any drilling
at all. There's already a hole in the sheet metal -- where I assume they spray
the foam in (?) -- so you can just cut through the foam and the plastic and then you
have your secondary entry point.
We've got the holes marked for our flange.
Again, you want to make sure you're at least eight and a half or nine inches from the
back edge to make sure you avoid that condenser line.
[ drilling resumes ]
That is the last of the drilling, and we're ready to mount our tower.
I also 3D printed plastic inserts for the holes that we drilled, just for appearances. One for the top one
for the back, and then corresponding pieces for the inside.
I'm using 1/4-20, two and a half inch hex head bolts with a flat washer on each side.
[ ratcheting ]
This is our final fit with two kegs and a five pound CO2 tank.
The tower that I'm using is a three inch diameter chrome ABS draft tower from Williams Brewing
with two Intertap tower shanks and faucets. The drip tray with the tower cut out
is also from Williams.
Your keg will have an inlet post for the CO2, sometimes
designated by a star-shaped base and the outlet post for the liquid.
The connection to the post is a ball lock quick disconnect -- black for liquid and
white for gas. They are not interchangeable. The way these go on is
to pull up the flange, pop it onto the post, and release the flange.
If your disconnects have hose barbs, you can attach the hoses directly. I prefer to
use the flare nuts.
the tower shanks have a 90 degree hose barb with a curved flange to match the
curvature of the tower, and then an associated curved insert for the inside.
You'll want to start by attaching the hose to the shank with a hose clamp.
3/16" inner diameter is the common size for beer tubing.
On the other end of the tubing, attach your flare nut, but do not attach the quick disconnect
just yet, as we still need to feed this down through the tower.
Make sure you have the flange on the outside, and then start feeding the tubing into the tower.
Before you feed it all the way down into the fridge, add your curved insert and the shank nut.
If you have a shank wrench, you can try and use that to tighten the nut, but...
it's a tight fit in the tower no matter what, so I always end up tightening it with some needle-nose pliers.
Then feed the lines down into the fridge.
We have some insulation to keep the beverage lines cold in the tower.
You can try and squeeze that in through the top, but sometimes it's easier to
just disconnect the tower and put it in through the bottom.
That's all there is to it! I hope this was helpful, and...enjoy your kegerator!
[ draft beer pours ]
Cheers!
[ ♫ Outro Music ♫ ]
[ ♫ Noir by S Strong & Boogie Belgique ♫ ]
© Zemba Craftworks 2017
-------------------------------------------
Un régime de pommes de terre : Perdez 3 Kg en 5 jours seulement! - Duration: 6:35.
-------------------------------------------
Rohff : quatre ans de prison requis suite à l'agression d'un employé de Booba - Duration: 2:28.
-------------------------------------------
Initial D: Flurry - Part #1 - Challenge from a Senior - Duration: 4:21.
Remember to drift in corners, hold left or right while pressing the 8 key, that way you can drift. Practice makes perfect.
Drifting can change the direction and speed of your car, but it won't change the acceleration. When drifting in the corners, remember to try not to lose time!
Challenge from a senior
After a drift you should accelerate quickly. Be careful not to drive off the road!
This is Usui pass......
Wow...... I haven't seen such a road.
It seems completely different from Akina.
It would be easier to see, why don't we have a race?
Okay, Iketani.
Takumi was so fast and powerful...... if I'm compentent to say that.
Fine.
Don't say that...... it's nothing.
It is easier to spin out in the rain when there is less friction.
-------------------------------------------
17 photos incroyables qui montrent que la naissance est la plus belle des choses - France 365 - Duration: 6:30.
-------------------------------------------
Volkswagen Passat (8) GTE Connected Series Plus Passat 1.4 160 kW / 218 pk PHEV Limousine 6 versn. D - Duration: 1:01.
-------------------------------------------
(Travel With Me) 미국에서 한국문화를 탐방하기 ▫ VLOG IN KOREAN ▫ Korean Culture in U.S.A - Duration: 13:21.
Hello Everyone. Today I will..
I wanted to make a video about my U.S. life
So today...
I will only be speaking only
in Korean (Imma finna try..)
Issa so hard (It is so hard)
Did I do well?
He said I did well
I am so weird
So now. First
We should eat
I am currently living in Virginia
There alot of Korean resturants
So lets go there first
개못생김 ㅋㅋ
Lets go
*LITTY music Playing*
I bought it
When I lived in Korea
It's so cool
Korea has all sorts of things
Of Course
It's hot
나 진짜 이상해...
Don't be embarrassed. You're doing well.
I am so embarrassed right now
Because I cannot speak Korean
Can you only speak in Korea?
Yes, Only Korean
I can't speak in English
*Screaming? Laughing? *
Today we didn't bring our sunglasses
The weather is too bright
So awkward
We have reached Annandale
Virginia, Annandale
We are hungry
We have to eat fast
What are you doing?
Trash DJ
What?
Skirt?
I didn't wear a skirt during my instagram live
You talked about what happens when you
Wear a short skirt
아 진짜?
까 먹었어
ah people stare at me?
Always
In Korea
and in U.S.
It happens alot
Tosokchon
Is here
He is wearing his shoes
He is over there
Should we go inside?
We have arrived in Tosokchon
There is this type of menu
*Naming the items on the menu*
What is this all called?
Soups?
Are they all considered soups?
There is also Bori Tea
When I was in Korea
This type of food
was so cheap
But here
It is so expensive
Super super expensive
$13
If you only eat Kalguksu (Korean Knife Cut Noodle Soup)
It is $13
But in Korea if you eat Kalguksu
It is around $5
Around $5
So sad...
In U.S. you need to give a tip
But in Korea you don't need to tip
So lucky!
You can hear me well, right?
You're Korean is better than my English
My Korean is better than your English?
But you English is good
Why is there barely no side dishes?
There is only this much
We should be thankful that there is something
He said Be thankful that there is something
There are these 3
And Bori tea
I don't know what this is
I don't know what this is
Dakgaejang (Spicy Soup with Chicken)
and
Bulgogi stew in an earthenware pot
The stone pot is called Ttukbaegi
We have to taste it first
How is the taste?
The taste is gooood
Also Spicy
This is not spicy
How is the taste?
It's good
But I have contacts on
I have to be careful (Because of the heat)
But it is delicioso
Come closer
*뜨거워 o * 떠워 x *
But it's so hot so I have to eat slow
But it looks like it will be good
Yummy
*목방 Mukbang *
Now let's go to The Face Shop
I usually
use Korean skincare
You can't see me? It's okei
Let's do this
So today I have to buy Cleanser
Cleanser, essence, toner
I also need to buy toner
Come here
Is there a good essence here?
*EXO- Kokobop*
I bought it~
Guess who I am?
My mom told me...
Always talks about what his mom told him
There is no mic?
So funny
We were talking about Show me the money 6
Rapper Black Nine
I seriously cannot do it
I sound like a crazy person
You sound like a puppy
The lighting here is pretty
Now we will go to H&M
Are you dancing?
He was dancing
Korean rappers
Female rappers
Always- Yooo~
Jessi always did that
*Unpretty rapstars quote*
Jessi is funny
Should we go to Sephora?
oh! They closed the door
They will probably close *sephora* too
When you are too broke to buy FENTY Beauty
So you just touch her poster...
She is so pretty
*Copying Woo Wonjae*
*Copying Woo Wonjae*
We are both trash rappers
L'occitane
Let's go to l'occitane
Is it l'occitane?
It's only that much?
All of it
*Drops*
What are you doing?
You messed up
*Just leaves it flat *
The movie is done now
We watched Kingsman (The Golden Circle)
There is no one left
It is currently 12 AM
Everyone went home so...
I should go home too
Kingsman (The Golden Circle)
I would recommend it . It was really fun
Right?
Kingsman is always
Super good
꿀잼~~
Now we will go home
Thank you for watching my video
There is a like button down below
And also subscribe
*Copying Woo Wongjae*
*Maleek Berry- Bend It*
-------------------------------------------
Playthrough: Avalon Code - Part 77 - Duration: 10:24.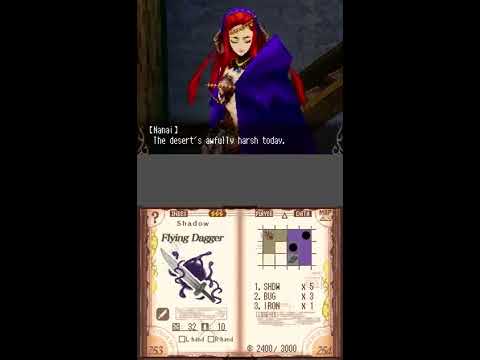
Last time Fro asked Yumil to get him a slice of Cream Cake from the castle kitchen: after this event a Metalize Tablet for it will appear in the Dining Hall...
...I don't think you have to scan all points of interest in the room for it to appear, but I could be wrong (I'd have to check all my pas videos, or wait until I get the Frannelle pages back ^^)...
...Anyway, the Cream Cake Metalize (1:40) is obtained by solving an easy sliding puzzle. The Item itself is the reward for this side quest...
...but it's not very good as a healing Item (3 HP for 50 MP); still makes for a nice Present for those who like sweets. We give it to Fro at about 4:00...
...and then get some MP back on the way out as usual. Skip ahead to 7:50
This is the last non-romance-related scene we can get with Nanai (as usual, just give her more Presents): we learn some more about what happened...
...between her, Olly, Ellie, and Anwar. She feels guilty about the disaster that happened, and especially about Anwar...
...Please read the whole story if you're interested. At the end Yumil is asked whether she should apologize to Ellie, and doing so will reveal...
...what you need to do to remove her Bind Code. We'll see about that next time though. Subtitles end here
-------------------------------------------
¿Exploración en casa abandonada? :v Ft, Miguel xd Parte 2 - Duration: 2:06.
-------------------------------------------
Drain Inspection Toronto ON 888-883-8588 Toronto ON Drain Inspection - Duration: 1:07.
Drain Inspection Toronto ON. Do you have Re-occurring sewer backups?
Not sure where your drain line goes?
Do you Suspect pipe damage?
Or about to Purchase a new home …then consider a professionally-performed
drain line video inspection.
The best way to understand your drainage system is to actually see the inside of the pipes.
There are a variety of high tech equipment which allows us, and you, to see what the
inside of your pipes look like.
An inspection is done by pushing a waterproof camera through the pipe while the technician
records the information.
Pipe size, material, joint alignment and other specifications are viewed.
Using this information, we will discuss specific long term solutions to solve your drainage
issue.
Call today to find out how we can solve your drainage problems.
-------------------------------------------
Urbex Belgium- The end of Château Miranda - Abandoned castle with huge history - Duration: 21:11.
good morning viewers, it's currently 4 o'clock in the morning.
Way too early!
We all got up at 3 o'clock, that's another hour earlier.
And for a special reason, for today we will visit "Château Miranda" for a third time.
And I think we get well on time because if the owner walks with his dog in the morning, I think you'd rather not be there.
We are going on our way and hope to arrive there for sunrise.
And we're very excited about it!
That's for sure!
Come on!
The grounds had belonged to the genus Beaufort de Celles (later Liedekerke-Beaufort) since the 11th century,
Who inhabited the castle of Vêves since the 15th century. In the 2nd half of the 18th century the Count left this castle
However, to live in a country house just a few hundred meters from Vêves.
This country house, which could best be called a castle, was also known as Noisy's country house
Later a more modest farm was built here.
The grandson of the Count who left the castle of Vêves decided not to restore the old castle.
In 1866 he commissioned English architect Edward Milner, known throughout Europe,
for the construction of a whole new castle that fit more with the taste of the 19th century.
Milner died before the building was ready. The French architect Pelcher took over his work.
The castle was built in a variety of phases over a very long period.
In 1907 the work was finally finished
Between 1939 and 1945 the castle was held by the German occupier.
After the Second World War, it was partly made available to the SNCB (Belgian Railways).
They converted the left wing to a holiday home for groups of children and youngsters while the digger continued to occupy the right wing.
In 1958 the Count finally left the castle to settle in the nearby farm.
However, since 1991, the building is empty and soon decayed.
Anno 2009, almost 550 windows were thrown into the castle and complete stairwells collapsed in some parts of the building.
The municipality of Celles has already made an offer to take over the castle and the land.
But the family did not want to leave the castle until now.
On February 5, 2015, the castle was removed from the heritage list, leaving it no longer protected from demolition.
A month later, a demolition license was submitted by the owner of the castle itself.
The demolition works began on Monday, October 24, 2016. But in early November the works were stopped again.
The demolition resumed in May 2017, but was resumed in June 2017
The Count, however, went to appeal and now...
Hi viewers, 6:30, arrived at Miranda.
For those people who have seen our previous film from Miranda, they will instantly know where we are walking.
There is the 'Château Vêves', but you can not see it now
We decided to arrive so early because we do not really know what security is like here, many stories have been heard
And it's cold here!
I see nothing more!
We must pay attention to the fact that we do not notice, because I think that everyone here in the neighborhood immediately advises the baron.
We appreciated it well, just sunrise.
Try to make as little noise as possible.
The second half, which was still there, has already been broken!
That's really deep!
Incredible, I think we are one of the last to be on Miranda's tower.
There's another part, there's everything left, we've got the drone, we'll fly around.
I keep finding it incredible.
But all the beautiful things come to an end.
So Kenny... this is your companion!
I think everyone remembers the pictures from our previous movie.
Then I took a picture of all these 4 holes
Here, of course, everything remains except that tap.
But these pictures are fundamentally changing.
It may be that these are the last images I'm going to make,
Because here it's really mega dangerous if I fall down here...
Mom, Dad, I've seen you guys
Tatti and all friends, I've seen you guys, but I just had to do this
For Kenny!
I just wanted to ask where to put my feet.
I would do the best backwards.
When I got up I saw something loose.
Hold right right.
Can I stand here?
You can stand there, yes!
That was the hardest!
All that dust!
It worked!
Normally it's really a bad idea to enter a half-broken castle with tons of rubble above our head.
But this is 'Château Miranda' and we will always be sorry if we have not done this
And I say that every time, but I'm afraid it's definitely the last time this time.
Look, that road we've done together with Kenny.
Then Kenny was there, he is also here, but we do not see him.
And if he shows himself, I will shoot.
The turntable
That was not the last time.
Still, it always stays a bit like an old friend.
That turbine has just been laid down here.
Above we arrived the very first time,
because then I filmed with the gopro and said, what is that?
Along here outside, we have been around.
Will that work over there?
It does a little strange.
It's weird to imagine it, but we've been walking around for 3 hours,
We watched the watch and shook a little bit
But yet I fear that this is the last time.
-------------------------------------------
Lockport IL Sewer Clog 815-630-1024 Lockport IL Sewer Line Clog - Duration: 1:09.
Lockport IL Sewer Clog. Are you sick of having your drains or sewer line rodded and paying someone to come out
every 6 months?
Tritan Plumbing has a long lasting solution to the problem of drain obstructions and tree
roots intruding into sewer lines.
We have a state of the art high pressure water jetter that cleans out grease, sludge, tree
roots or any other blockages in your pipes.
While rodding only pokes a hole in the clog, water jetting cleans out the entire surface
of the pipe.
We are trained experts in sewers, drains, and septic systems.
We'll stop your problem at it's source and keep your home safe.
To get a better view of what's going on, our technicians can do an in-pipe camera inspection.
If your drain is blocked and causing issues, emergency service is available.
Give Tritan Plumbing a call today, we'll get there fast!
815-630-1024
-------------------------------------------
Dancer's Ways | WINDS - SHAPES FROM NATURE (Trailer) | Online dance school by Illan Rivière - Duration: 1:14.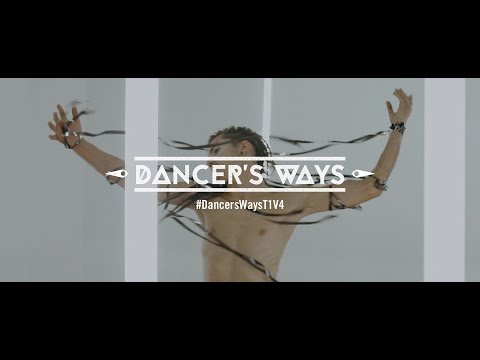
Winds, invisible, They are born from change, they are the consequence of the movement.
Let us feel, simply, the air that touches our skin.
Let yourself be influenced by breezes of random directions, by the gusts that challenge you and flatten your clothing against the skin,
Imagine yourself as a rock that cuts the air path.
Like a tree firmly anchored in mindfulness, you lean against the gusts,
lean on a flurry, push currents, block, resist, play with opposite directions.
This time the air passes through you, your body becomes a filter, a passage.
Imagine the air seeping through the pores of your skin, through you completely, you become permeable.
Look forward to storms, run against the winds, move on infinity,
radiate the horizons with light the winds will do the rest.
-------------------------------------------
Ford Fiesta - Duration: 0:52.
-------------------------------------------
ALL about my Stretched Lobes || HUGE 00G Plug Haul - Duration: 4:16.
ALL about my Stretched Lobes || HUGE 00G plug haul — By Victoria X Rave
hi guys it's a choice right here Victoria or what Victoria X Rave can you
spell that Victoria X Rave a the X Rave like an egg
no X Rave I need to change my name to drive here and I want to talk today
about my stretched lobes these plugs first off I have a video of me actually
stretching them to this size from like a year ago I've had them in this size for
a year now whoa so it's zero zero gauge right now and that's probably biggest
I'm gonna go honestly I don't know have a reason to go bigger the biggest con to
them is that everyone with stretched lows will understand this if you don't
have them don't judge but they just don't smell good I watch them every
single day they're finally healed to the point
where I can take him out every day first like half a year they weren't healed
enough to take them out consistently but they're fine now so where I can do that
and I could change them and blah blah blah but it's really not they're not
that big to where they cause up of your problem if I have like huge ones like
some people do I don't know how they were like headphones like how do they do
that I don't know I mean my ears are very small so I want to show you guys
all the different types of jewelry that I have for them this video is sponsored
by evevil plugs and you can get 20% off with my code which is only gonna last
for a month down in the description and you can get them off of Amazon they're
actually like really nice plugs these are the kind that I use they come in a
box like this and I got like a whole a whole pack of them the thing is is that
whenever you wear plugs like you need to match them to your outfit this is what
my ears look like without them I like this set because they have like
every single color and every single like style you see them okay so let's open
these and I'm just gonna go ahead through all them and show you what they
all look like right now since I'm wearing black I'm gonna start with black
voila these are the black ones
let's show all my jewellery ready get set
so now it's kind of like a full plug haul but like there's so many of them
there's ones that are heavier there's ones that are lighter like this is a
heavier one it's like a black and then there's there's light ones but it's like
this one's black but it's also like super super light I would recommend to
sleep in with maybe a lighter one like these ones and then there's they have
sparkly ones it's I don't know if you guys can can tell on camera so there's
there's 18 pairs in this box so link down below check them out they're pretty
cool I like my stretch lobes you stretched it with a taper and you guys
don't know this isn't really a tutorial of how to do it sighs we kinda wanted to
show you this this pool hall of all these these different plugs that you can
wear with different outfits if you're thinking about stretching your lobes
just know that it does take a long time you have to leave a lot of time in
between and stretchings to let it properly heal I recommend getting
stretched lobes if you really want them make sure you see this commitment and
just make sure that you follow the proper healing time wash them and just
upkeep them because it's a little more effort any any type of body modification
it requires a little more effort with piercings stretch lobes hair whatever
it's just a little extra a little extra the loom alright guys I hope you stay
super Extra Terrestrial now this video is pretty short but I
hope you enjoyed it anyways make sure you subscribe right here all right
ALL about my Stretched Lobes || HUGE 00G plug haul — By Victoria X Rave
-------------------------------------------
Dunkle Wintermonate: Wer braucht zusätzliches Vitamin-D? - Gesundheitsnews - Duration: 6:33.
-------------------------------------------
Un régime de pommes de terre : Perdez 3 Kg en 5 jours seulement! - Duration: 6:35.
-------------------------------------------
Bretonische Insel Windig, schroff und abgeschieden - Duration: 12:08.
-------------------------------------------
Best in Class CoreSite Data ...
-------------------------------------------
Skrillex x Habstrakt - Chicken Soup (MY BAD F#*K UP) - Duration: 2:34.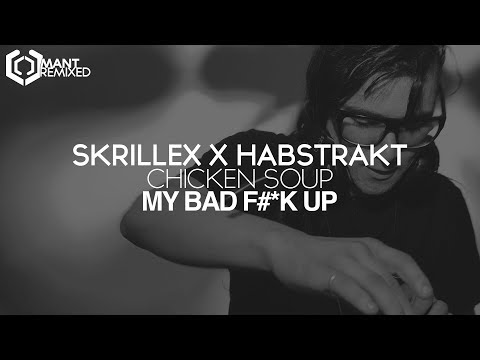
Skrillex x Habstrakt - Chicken Soup (MY BAD F#*K UP)
No comments:
Post a Comment