Hello and welcome I show you today how to cook cheese easy
can produce quickly and cheaply the cheese cook tastes very delicious for
a spread spreading to boiled potatoes as a dip or as a basis
for cheese soup or cheese sauces and here are the ingredients
125 grams "Harzer Käse" 250 grams Quark 100 grams of butter 100 milliliter of milk or cream
one teaspoon soda half a teaspoon of salt and a little
caraway to taste. First, cut the cheese into cubes harzer
if you cut the Käs into small cubes
then it releases later in the heat more easily and enter the same in the pot
then the butter and also enter the milk in the pot and on the
go herdplatte and heat the whole
now all over medium heat warm up butter and cheese melts, stirring constantly
and now takes a few minutes you see it melts beautifully
the cheese is also beginning to melt at my herd I warm the earth
always on stage 5. Now as long stir until even the harzer cheese completely
is dissolved and it took about four minutes
when everything is resolved, add the quark
and stir until also the curd has completely dissolved.
when the curd has dissolved completely turn off the stove ever
and thus the cheese also remains permanently spreadable, adding the soda to
and before adding the soda, nor spice cumin and salt with the
now caution the release of soda that something foams now
is important to take a large pot, so it does not overflow with the addition of soda
Stir well the soda. if soda is combined with heat and humidity
it reacts and the mass goes up.
again stir well and let the cheese cook is ready to be bottled.
now decant the cheese cook the same in hot rinsed glasses
make sure that the edge is clean and close glasses equal
my husband has already prepared the appropriate label
the cooked cheese sticks kept for about 10 to 14 days and is important to always refer to the cheese cook with a clean knife.
making it a try for - bye and see you next time
For more infomation >> Kochkäse / Dip / Brotaufstrich - Duration: 4:28.-------------------------------------------
INCREDIBIL, s-a aflat adevăratul motiv pentru care Laura Bretan a ratat Eurovision! Specialiștii au - Duration: 4:53.
-------------------------------------------
Frontline Fashion 3, with Cara G Mcilroy: Episode 5 - Duration: 11:26.
It's been three months since Tess won the first prize
in the 2018 Redress Design Award.
Her prize was to design a sustainable collection for the label The R Collective,
and her mission to take it to market.
Now has she been able to do this?
Let's find out.
Hey guys! Hey Tess!
Hi!
This is so exciting!
Yeah it's insane.
Oh my God, so it's only been three months since you won
and already we're here at the photoshoot for your collection.
How has the journey been?
Pretty stressful, like there's been a lot of challenges but I've learnt so much.
- I'm sure. - So it's been a pretty full on three months.
The Redress Design Award 2018 with The R Collective goes to...
Tess Whitfort!
Tess won because her technique is very, very well done,
and also her style is very original.
I'm really excited about my journey ahead with The R Collective
and it will be so fantastic to have so much guidance on that journey
to making my first commercial collection, yeah.
Our last collection is in Lane Crawford.
Oh cool!
The next day, straight after the finals we had our first design meeting.
With The R Collective we are doing six capsule this year,
and yours is actually the first one.
The R Collective is started by Christina Dean who is also the owner of Redress
and it's a fashion label that is all about up-cycling.
What you doing today Christina?
I'm going to be a model.
I would say like the reason why we have to work extra hard
is because we really try to stay away from making waste look like waste.
It has to be like extra luxurious.
What's kind of your vision for this collection?
We are thinking about doing a six to seven piece collection.
We wanna make sure all the pieces could be mixed and matched
with the client's own wardrobe as well so nothing too crazy,
nothing too dated, definitely 'timeless' is our key.
I've always done more artistic, edgy kind of collections
so it's quite a different target audience.
So what's the timeline for this collection?
We are aiming to launch in February,
which means all the samples need to be done by November.
That's pretty tight, yeah that's a short timeline.
Yes.
I think it's going to be very challenging.
Oh she's got some hard brutal work to do,
she's gonna be working non-stop.
So I started designing while I was in Melbourne.
The starting point was thinking about ways of incorporating my style
with The R Collective brand.
So it's all about like streetwear,
in a refined wearable context.
I was communicating with The R Collective.
So I was emailing them sketches and then at the same time
we were looking at the textile waste that was available
and selecting things that were appropriate for the designs.
So my collection is being produced by TAL.
Most of the textile waste we are using is sourced from a factory in Bangkok,
like industry end-of-roll fabrics that other brands have over ordered
or have been left to move excess inventory.
so we're taking that and re-purposing it into something desireable.
So all of this is available textile waste?
Yes.
That one as well?
Yes, same.
The fashion industry produces an estimated
four hundred billion square metres of fabric every year
and for various reasons,
up to fifteen percent of this ends up
on the cutting room floor.
One of the main culprits is fabric left over
after the pattern is cut.
Zero waste design eliminates this problem
by creating a design and pattern
that uses a hundred percent of the fabric marker.
To do this a huge amount more thought and planning
is required at the design stage
as measurements must be exact.
This can be quite cool for the jumpsuit actually.
Do we know the width?
Fifty eight.
So that will work well because we need the width
to be the same to do the zero-waste pattern.
Yeah, that should be good.
Alright, what else have we got?
With the zero-waste pattern cutting
I think it requires working within parameters
that are set by the techniques and materials that are available.
I'm thinking about using this fabric for the pants.
It's got like a little bit of texture to it which is quite nice.
The content isn't ideal,
I like always prefer to use natural fibers
but working with textile waste
we kind of have to work with what we got.
This is cool. I like the colour.
Is this cotton?
- Yes. - Nice.
Do you think the consumer will like it?
It is a little bit rough,
but I think in like an oversized t-shirt it'll be ok.
Yeah, I think this will be really cool.
Ok we have some fabrics, that's a good start.
I only had a couple of weeks to actually design the collection.
I'm a fresh graduate!
I've never created a collection for manufacturing before
so I'm still quite worried that we weren't going to meet deadlines.
I did feel a little bit stressed.
The team from TAL came to us in Hong Kong
and we viewed the first samples.
We were kind of looking at the samples
and we were like 'oh they look fantastic!'.
Nice huh?
Yeah, super nice!
Trying them on the model,
and they were fitting really well.
I'm all about pockets!
But once we look at the pattern...
It's not zero-waste.
We realised that the samples were not zero-waste.
We actually opened up the markers
and realised that they've just conventionally pattern cut them
according to the sketch and the measurements that were provided.
Zero-waste is so new!
I think the factory just have a very systematic way of doing things.
They immediately, you know, think in their head like
'ok, how do I transform this sketch into a sample?'.
They don't expect you to give them how to draw the pattern.
So I think we need to go a bit more detail style by style.
Ok, so we need to cut where?
Where's the cutting point?
This should probably be a dotted line, that's a fold.
Ok, fold one.
You need to work on the pattern.
Because you don't give them more specific measurements
then it's very hard for them to work.
It's really difficult to alter conventional patterns to zero-waste.
You kind of have to start from zero again.
When I first arrived back in Bangkok,
I then created the whole zero-waste pattern marker
and did the whole layout with multiple sizes.
And I think from there they did understand the concept more
letting go of those sort of rigid rules that are usually applied to pattern cutting.
What did we change?
This wasn't zero-waste.
So we developed the zero-waste patterns,
we made it longer...
and now we're going to see it in the actual fabric.
Yeah, it's exciting.
The team at TAL turned out to be just like, so helpful.
Their sort of technical knowledge and ability to problem solve
was really valuable.
She said you can even do a flap for access
from the leftovers.
I think as long as we get the shell right,
then we can tailor the details.
Yeah, she gets it.
I think with the zero-waste technique,
it was something very new for them.
But once they get it it was a lot quicker than us doing it.
Can we cut, like, this on one of the one and a half yards,
and then this on the other?
Ah...
it can do, but very, very difficult.
They also use a lot of computers to do the calculation
which we don't know how to do,
so I think there's definitely an advantage there
of working with someone like TAL.
In just one week, it really turned around.
They've done a good job of that.
They've done a really good job.
The samples looked really good
and the zero-waste patterns were working
so I felt pretty good about it by the time we left.
Today we're doing the photoshoot for Tess's collection
because now the samples are done,
now is like, really thinking about how to market it.
It's nice to have lines because of the weave of the shirt.
With sustainable fashion,
the way you market it is different
because you have to explain the story behind each product.
That's good.
Yeah, perfect.
Yeah, these are cool.
Ok, change!
So what do you think about the collection?
I'm really happy with it.
It's kind of a product of the textile waste that we're working with,
the zero-waste patterns,
and combining my style with The R Collective.
- Yeah - So what we've ended up with is a good mix.
Yeah, that's good.
Yeah, I really like it!
I think it gives The R Collective aesthetic
and also puts a little bit of Tess in it.
Beautiful!
Very proud of it.
But to secure a buyer is very, very difficult.
The biggest thing I've learnt is
it's really important for us to actually integrate
sustainable techniques into the fashion industry as it is today,
rather than thinking of sustainable design as bit more of a niche.
We need to look at ways of making sustainable fashion profitable
and applicable to all aspects of the fashion industry.
We've now learnt how important it is for designers
and manufacturers to work together
to lessen the impact that fashion has on the environment,
and we as the consumers are the last piece of the puzzle,
and it's easy to get started!
We can swap clothes with our friends,
we can ask more questions to the brands we buy from,
we can invest in timeless pieces that
we'll love and cherish forever,
and of course we can support sustainable fashion designers
in their fight for a brighter future for fashion.
-------------------------------------------
Fosta iubită a lui Gabriel Cotabiţă s-a măritat! Cântăreaţa Dalia Puşcă e în al nouălea cer: „A fost - Duration: 2:53.
-------------------------------------------
ADEVĂRUL despre lacrimile amare vărsate de "faimosul" Costin Gheorghe la Exatlon! Sora lui a spus to - Duration: 3:37.
-------------------------------------------
Tạo nguồn thu nhập thụ động 500$ mỗi tháng với Futurenet - Duration: 12:34.
-------------------------------------------
Dragon fruits roots as fertilizer | Dragon fruit rootstock | ছাদকৃষি | YT |#momtazgarden - Duration: 3:30.
Dragon fruits roots as fertilizer | Dragon fruit rootstock | ছাদকৃষি | YT |#momtazgarden
Dragon fruits roots as fertilizer | Dragon fruit rootstock | ছাদকৃষি | YT |#momtazgarden
Dragon fruits roots as fertilizer | Dragon fruit rootstock | ছাদকৃষি | YT |#momtazgarden
Dragon fruits roots as fertilizer | Dragon fruit rootstock | ছাদকৃষি | YT |#momtazgarden
Dragon fruits roots as fertilizer | Dragon fruit rootstock | ছাদকৃষি | YT |#momtazgarden
Dragon fruits roots as fertilizer | Dragon fruit rootstock | ছাদকৃষি | YT |#momtazgarden
Dragon fruits roots as fertilizer | Dragon fruit rootstock | ছাদকৃষি | YT |#momtazgarden
Dragon fruits roots as fertilizer | Dragon fruit rootstock | ছাদকৃষি | YT |#momtazgarden
Dragon fruits roots as fertilizer | Dragon fruit rootstock | ছাদকৃষি | YT |#momtazgarden
Dragon fruits roots as fertilizer | Dragon fruit rootstock | ছাদকৃষি | YT |#momtazgarden
Dragon fruits roots as fertilizer | Dragon fruit rootstock | ছাদকৃষি | YT |#momtazgarden
Dragon fruits roots as fertilizer | Dragon fruit rootstock | ছাদকৃষি | YT |#momtazgarden
Dragon fruits roots as fertilizer | Dragon fruit rootstock | ছাদকৃষি | YT |#momtazgarden
-------------------------------------------
방정식 함수 미적분 기하와 벡터 공부 잘하는법 토론수학 공부법 코디 중2수학[건강한학습연구소] - Duration: 1:34.
-------------------------------------------
Литые диски RW H-497 цвет DDN F/P - Duration: 1:33.
-------------------------------------------
Литые диски RW H-125 цвет DB F/P - Duration: 1:31.
-------------------------------------------
Литые диски RW H-497 цвет BK F/P - Duration: 1:35.
-------------------------------------------
Литые диски RW H-417 цвет BK F/P - Duration: 1:35.
-------------------------------------------
ЛУЧШИЕ КАМЕРЫ НАРУЖНОГО ВИДЕОНАБЛЮДЕНИЯ С АЛИЭКСПРЕСС - Duration: 8:48.
hi to all you on the channel ava today in our review the best cameras
outdoor video surveillance with aliexpress Chinese video surveillance equipment
proved its quality and performance in the most complex
conditions to buy api camera on aliexpress is really beneficial price
similar devices in offline stores while still significantly higher for outdoor
video surveillance is used as simple and cheap cameras and more advanced
wired for this and devices turning zumman all are configured
from your smartphone to improve the night vision uses infrared
illumination of the new generation are LEDs do not fail for longer
rating we have included a variety of models they have in common is the best
value for money
number 5 railing Argus 2 + solar panel better autonomy even wireless
devices for video surveillance power required
and this cable and which not always can be give
this camera from our review is different battery life the device runs on
solar panels and the seller with aliexpress sends with the gadget
the device interacts with the smartphone via Wi-Fi model can
used as a video call with two way communication
as well as the siren alarm removable the battery has a capacity of 5200
milliamp hour you can charge it from network adapter with powerbank
or solar powered the power of the panel itself is only 2.8 watts
cable long plug USB have protection from moisture
the picture quality of this model is worthy with the proper settings entry
occurs only after triggering motion sensor in the rest of the cameras
can be in standby mode just note that the device can not
connect from smartphone without Internet
number four is real 420 is great detail video camera for those who
appreciates high quality video shooting the device is something
average between home gadgets use and complex design
equipment model shoot video in high resolution 2560 at 1925
megapixel camera with the most detail even when zooming in, the picture turns out
quite detailed can be consider small details on a large
distance the number of machines the faces of the people there are great
protection against external weather factors ip66 and built-in memory card slot
connection and PI of the camera is carried out on power technology on ethernet p minus
one cable is used for video and audio
block Wi Fi this modification is not but it's not a scary bit to watch out for
events can be at any distance through the app real to on your
mobile device built-in nvr digital video recorder
allows for covert surveillance 24 hour per day
build and playback quality video is one of the best cameras in the review
number 3 x and link VAT 2 de 3300 4wd optimal combination of quality and
speed video the company hike the entire and it is in second place in the world
among the systems of video surveillance and after Hua
and if you have serious demands image quality and functionality
then take a look at this dome the peak of the world from our review is simple
installation setup and maintenance 4x zoom
open ONVIF network interface support micro sd card up to one hundred twenty
eight gigabytes and many others this utility offers
manufacturer there is a notification on the smartphone when
the penetration of the camera object lightning sums perfectly smoothly
moves quickly fades out of focus quality is felt even in materials
Assembly therefore products from Haik mission popular among professionals, it is often
use for covert surveillance this the device is really better and it
will work for many years with care circulation price is higher than Wi Fi
modifications with aliexpress but ptz cameras ensures a clear stable
the video signal which is not say about wireless models working on
air
number two. stark c7000 815 wrp rugged case
IP camera in stark c7000 815 specially designed for outdoor
observations she is not afraid of the scorching sun
the bitter cold is not pouring rain metal case is strong enough
to protect the device from vandalism and its sealed design will not allow
dust and moisture ingress standard ip66 protection
protective visor and easily adjustable therefore, the quality of the video will not suffer from
drops on the lens and sun glare the device is mounted on a wall or ceiling
with the help of bracket which can be change the angle of inclination and turn in full
dark shooting is carried out on distance up to 15 meters since
the device is equipped with thirty infrared LEDs to
the advantages of users include automatic switching sensor
mode's day-night and presence of the module Wi-Fi
however, there is also a disadvantage may occur difficulties when installing micro sd card
number one hang it x d 54 f30 x reliable swivel camera with the best
zoom is a good PTZ IP camera which can be purchased on aliexpress without
space charge the model was included in the review due to
qualitative summation of the picture and supports remote management in
description of the 30x zoom but in fact it ten times but it
also a decent number of car numbers read at a distance of about 100 meters
the site has several options for the model with a resolution of 245 megapixel angle
view in the area of 60 degrees of rotation 360 the device can see 50 degrees in the dark
meters can be used it for covert surveillance PTZ camera
can be installed on the street have it automatic tracking function when
motion detection it will lead the object of the functionality of the device
able to replace two fixed models have another feature of the device
digital noise reduction image smoothing in case of bad
lighting or rainy weather allows you to get high-quality video
frost and heat the device is not afraid of running smoothly
and at -40 and at plus 50 degrees
we hope you enjoyed and appreciate this video by clicking on like subscribe
the channel is ava it was a review of the best outdoor camera
video surveillance from aliexpress thanks to all who watched the video before
the end of all until meeting
-------------------------------------------
Antonio Rudiger admits Chelsea are low on confidence after poor run - Duration: 5:49.
Chelsea defender Antonio Rudiger has described life under beleaguered boss Maurizio Sarri as a return to the classroom and conceded players can become mentally tired
The picture of an increasingly fractured dressing room was underlined when Rudiger was asked whether Sarri's habit of asking players to train on the morning of games was having a negative impact
The 25-year-old German said: 'Fatigue, no, because it's not like we are doing box-to-box runs
It's not physical. It's the tactical things he likes to do. That's his way, he's carrying on
It's new for the majority of the players but we have to adapt to it.' LAST SIX RESULTS Feb 18: Man United H 0-2 (FA Cup)Feb 14: Malmo A 2-0 (Europa League)Feb 10: Man City A 0-6Feb 2: Huddersfield H 5-0Jan 30: Bournemouth A 0-4Jan 27: Sheff Weds H 2-0 (FA Cup) Asked if it becomes mentally tiring, Rudiger said: 'It's the same if you sit in the school the whole time listening to someone
Of course, sometimes, it gets mental, but at the end of the day you have to do your job
'Rudiger also conceded confidence is low, adding: 'We are always working in training, trying to do better each day
I think, right now, it's about confidence. It's not a tactical aspect, in my view
It's confidence. We are underperforming.'Rudiger believes that the the moment of reckoning will come in the next two games, against Manchester City in the Carabao Cup final on Sunday and Tottenham in the Premier League the following Wednesday
He said: 'On Sunday, a big game against City at Wembley. That will show the truth
That will show our way this season. It will be the truth in terms of keeping up with opponents like City, and also Liverpool and Tottenham
' Asked if the players retain faith in Sarri's style of play, Rudiger said: 'I'm not the coach, I'm a football player
This is something the coach has to decide and we have to follow.'You always play for your manager, but you want results
You want to win. No player on earth likes to have the kind of run we have had.' Sarri is clinging to the Chelsea job by his fingertips amid a dreadful run of form
Chelsea have suffered humiliating defeats at Arsenal, Bournemouth and City in the league of late, while they also crashed out of the FA Cup against Manchester United on Monday
Tonight in the Europa League they face the relatively straightforward task of finishing off Malmo at Stamford Bridge after winning the first leg in Sweden 2-1
Sarri insisted he has not held talks in the past few days with owner Roman Abramovich or his most senior director Marina Granovskaia
'No, not this week,' Sarri said. 'I have to think that I will be the manager of Chelsea for a long time, otherwise I cannot work
I am not sure (it will work), but I have to think this. I want to work with a long-term target
'Sarri also rejected supporters' criticism of his predictable style of play and his decision against United to replace Cesar Azpilicueta with another defender, Davide Zappacosta, when his side trailed 2-0 and desperately needed goals
Sarri said: 'The system is a false problem. I know very well that when we are losing I have to put a striker on the pitch
When we are winning I have to put a defender on the pitch. But I want to see football in another way
' Despite Sarri's persistence, Chelsea are believed to be considering a change of manager and defeat against Malmo or City may be enough to sound the death knell on Sarri's reign ahead of the crunch home game against Tottenham
Chelsea are understood to have major reservations about Sarri's assistant and club legend Gianfranco Zola, even as a short-term fix, and Paulo Ferreira and Eddie Newton may be preferred in the event the Blues require a caretaker boss
Sarri also faces a nervous wait before naming his team for the Carabao Cup final, as goalkeeper Kepa Arrizabalaga has a hamstring problem
Asked if the Spaniard will recover, Sarri said: 'I'm not sure, but I hope so.'
-------------------------------------------
[악의대부]사인(死印) - 제 1장 : 하나히코 군 #.1 (한글자막) - Duration: 24:15.
-------------------------------------------
Lexus IS 300h Hybrid Business Line - Duration: 1:23.
-------------------------------------------
最新ニュース 思春期にホームレス生活、異色女優の波乱な履歴書 - Duration: 7:57.
単独インタビ ーで心境を語る ーサ・サラザー (撮影・中島郁 ) ローサ・サ ザール単独イン ビュー 映画「 リータ バトル エンジェル」( 2日公開) ホ ムレス生活を経 ハリウッド大作 主役を射止めた 優がいる
「アバター」「 イタニック」で られるジェーム ・キャメロン監 (64)が製作 た映画「アリー バトル・エン ェル」(ロバー ・ロドリゲス監 、22日公開) ローサ・サラザ ル(33)
来日した異色の 星に話を聞いた ◇ ◇ ◇ - ーション・キャ チャーという手 で、あなたの動 は変換され、劇 にはサイボーグ して登場します 生きた人形のよ なアリータ(役 )をご覧になっ いかがでした
「オーディシ ンで出演が決ま たことも驚きだ たけど、独特な 界観の中で、私 分身が動き回る 像を見た時は、 う言葉にならな った。表情、動 …私のエッセン がそこに抽出さ ていて、本当に の世界で動き回 ているように思 ました」 -木 ゆきとさん(3 )のコミック「 夢」が原作です
日本的なものを じましたか。「 定はアジアでは く、人種のるつ のようなところ でも、日本の『 ンガ』らしく、 っすぐに真心が もったところが って、登場人物 ちが触れ合うい んなエピソード そんな日本の優 さを感じました -表情が豊か すね
それが劇中のア ータにも反映さ ていたように思 ます。 「子ど の頃は部屋にこ り、ぬいぐるみ 前でお芝居して き顔や怒った顔 していました。 な子ですけど、 の頃から演じた という衝動があ たんですね
女優になるのが 命だっていう意 はずっとあった ですけど、なか か家族や周りの に言い出せなか たんです」 - 優に踏み出すき かけは? 「1 歳で家族を離れ 独立しました
高校を出た17 から2年間、ア リカ中を回った です。ありてい 言えばホームレ 生活です。救護 設にお世話にな たこともありま 。こんな私です ど、名門大学に っている友達も て、各地にいる んな人の部屋を り歩きながら、 露をしのぎまし
私は『カウチ・ ーフィン』と呼 でいたんですけ (笑い)。みん 守護天使みたい 人。生活費を稼 ためにワシント DCでバーテン したこともあり した。19歳の にそんな友達の 人からニューヨ ク行きを薦めら 、背中を押され 形で本格的な女 修行を始めたん す」
-ホームレス 活で絶望的な気 ちになったこと あったのでは? 「もちろんです 純粋さを失った 思う時期もあっ し、思春期まっ だ中ですから、 いっきり落ち込 こともありまし
いろいろトラウ を抱えて、鏡で た自分の顔が今 り老けて見えた ともありました でもどん底を経 したからこそ、 の後、女優修行 打ち込めた気が ます」。 -ニ ーヨークでいく かの短編映画に た後、8年前に サンゼルスに移 てから「メイズ ランナー2」や ダイバージェン NEO」で役 付くようになり した
「そうですね どんな作品でも ずっとアクティ でいられたのは 0代の経験があ たからだと思い す。今回も撮影 6カ月前からマ シャル・アーツ どの訓練に思い きり打ち込めま た
ハードなレッス があっても、い でもどこでも眠 ことができる特 がありますから 笑い)」 ◆ア ータ バトル・ ンジェル 世界 を破壊した「大 」後の未来は、 空に浮かぶユー ピア「ザレム」 、そのザレムか 排出されたくず が堆積した荒廃 た街「アイアン ティ」に分断さ ている
アイアンシテ で「サイバー医 」として暮らす ド(クリストフ ヴァルツ)はあ 日、くず鉄の山 ら少女サイボー の頭部を発見す 。それは大戦中 失われたテクノ ジーを満載した 最終兵器」の中 部分だった
イドによって 身を再生された イボーグは亡く った彼の娘と同 「アリータ」と 付けられ、しだ に能力を発揮し める。 そのハ テクにザレムか も魔の手が伸び 次々に強敵が現 るが、やがては 女の力が分断さ た世界を揺り動 し始めて…
◆ローサ・サ ザール 198 年7月16日、 シントンDC生 れ。24歳の時 TVシリーズ「 AW&ORDE LA」に出演 て本格的に女優 動を始める。サ ドラ・ブロック 演のSFスリラ 「Bird B x」(NETF IXで配信中) も出演している
-------------------------------------------
TWO SHIPS PASS IN THE NIGHT - TRC AND TRUCKER RUDI - Duration: 11:35.
looky here everybody mr. Rudy has stopped by with us
how you doing Rudy I'm doing pretty good you fabulous bad girl you know you're
enjoying this snow heck yeah I like me some snow as long as the roads don't
close yeah that's the one worried but I heard up in Wisconsin they already got
about three inches of snow up there is what I heard and we don't want to go
that way no this is probably number two you right this is chickenshit for me you
always have your snowshoes on oh yeah for sure yeah well we're gonna cook up
some dinner you guys are welcome to stick around and meet with us all right
all right dinner is ready we're gonna eat this
dinner up y'all want to see you it's pretty good-looking yeah and then we're
gonna do a video video for you guys say hi girl
okay everybody let's talk to Rudy for a little bit you know what's up guys where
are you headed today well we're heading to Thunder Bay Ontario on our wait that
way anyways but right now we're in Chicagoland
Thunder Bay that sounds like fun water it is pretty close to water yeah yeah I
go all the way up to oh Claire Wisconsin I head to 53 and go up to Duluth
Minnesota and then I took believe it's highway 2 it goes all the way alongside
the lake up there and that goes right up to Thunder Bay up
there that's pretty cool you're an international player
yeah I am definitely an international crossing the border yeah no we're just
down here regular aisle boring people I'm not wearing Chicago I'd like getting
out of here safely yeah don't worry it is a lot of fun it's kind of exotica in
a way right yeah it is yeah like if you have ever seen me cross at International
folds mm-hmm you have yeah yeah there's a basically we cross on the same bridges
with the railway goes over oh that did it yeah
do they make your check and like you can things are cheaper to purchase down here
in America right that used to be true but it's not so much anymore there is
still a few things that might be cheaper but because the dollar is so high right
on the US dollar it's like 1:30 Canadian compared to the US right now so that's
like 30 33 percent difference so if you if you consider all of that and you
factor all of that into it things aren't so cheap anymore yeah I guess that look
at yeah I know but in the past I've talked to people that said that was a
big difference for certain items yes for certain items that might still be but
for pretty average things that you might be shopping for it really isn't
much of a difference anymore and you look at snowing out there right this is
just like baby steps for you oh yeah exactly for us this is this is nothing
especially if you drive up in Ontario and stuff like that way worse up there
or no Manitoba like or you saw the video where we did he was in Fargo there
mm-hmm that was that was much worse than what
we have today I think you win over 5000 subscribers other day you're hot you're
burning it up streaks out we try we try well you do some really good content
you're filming and takes your work is just fabulous oh thank you appreciate
that we do try our best we we have some good plans lots of plans for this summer
we planning on going to the truck show and Louie well if nothing goes wrong and
then it's summer we want to do some camping already got some plans for our
trip plans for camping and stuff so hopefully we'll get some good footage of
that get the drone out yeah I'm good drone flights out there
and hopefully you can get some good nice pictures again like you seen my sunrises
and sunsets I think that video were you and Chuck a jukebox was chasing each
other with the drones that was fine yeah we need to do that again now that would
be kind of fun to do yo we got a gremlin dog over here yeah that's just his
nature you know it's like that old adage about the the turtle and the support
beam you know whatever and at the end the tree
you know turtle saves the Scorpion and the Scorpion kills it anyway yes
yeah so that's kind of what we have planned for this summer hopefully we can
make good on all of that hopefully everything will work out that way and
even got Rudy on our mast just the ends right Rudy's gonna feel left out the
heaven map it's at home another home yeah that one goes up at the Canada yeah
he's just took the part of America that is yeah it is
well I'm looking forward to to summer again that I can't wait well you know
you'll see it before your your people's will up there yeah I will yeah
I always get the wife jealous Peschel if we get a nice hole going south I always
make sure I send their pictures it's nice and warm down
when does spring and why come on say spring I mean like typical spring
windows bud start coming on the trees usually May yeah
by May long weekend usually oh that that's not so far different you know
that our weather yang story she minute yeah I mean the snow is usually all gone
by by end of March maybe April mid-april usually it's most at time it's all gone
I mean we have time to where we still get snow and June these it is the
weather the same as when he was a kid well see I didn't grow up in then Canada
what I was you when you moved I was actually already married
I was 19 when we moved to Canada well that's been a few years ago yeah I was
in 2001 and so you might tell me where you grew up some people may not know
yeah sure I can do that I was born in Bolivia and shortly after
I was born my parents moved to Paraguay so for for most of my
young girl years I was living in Paraguay until I was 10 years old and
then we moved back to Bolivia for 4 years and then we moved back to Paraguay
again and so then you know I started working and stuff and then shortly after
that I got married moved to Canada 2001 just after 9/11 yeah yeah we were
actually delayed a little bit because of 9/11 I'm I didn't know the flights were
all shot down right only airports were shut down all in the world and that was
that was interesting Rudy speaks high German and Spanish and a little bit
France but he won't talk about it no no I don't speak no French but I do speak
Lord German High German a little because he can say partly Lou fronts like that
bit
not really but no if you can speak German you speak French though because
there's so much Carlos Spanish as I should closer to that's what I mean
because it's got elements of both yeah yeah yeah like like especially the
numbers like keen says is very close to close to the French 1,500
I found it there with me this is weird because I'll try to communicate with
anybody right sure with whatever I got to use and when I go to Mexico or
something that look at me like that's not how you say it you know what I like
did you understand close enough yeah I insulting your mom or something yeah
yeah but no so that's that's how I grew up and I'm always been living in Canada
since 2001 we I'm married and we have two kids
our daughter is his handicap so she's in the wheelchair so she did okay yeah
she's doing okay yeah because she actually likes them videos and all she
loves the attention like any woman does yeah and so yeah she loves she loves it
when she can be on camera so we you know we make daily vlogs pretty much every
day anyways the all day we've limits a day here and there but you've had mom
out on the truck with you a little bit ago
night sure did she enjoyed it she enjoyed it that's good oh yeah we had a
good time and we got lucky that we got the nice trip going to tax
one way I always always nice yeah it was that was like summer weather for Canada
oh yeah everything artic blast wasn't it what Sun that was during the artic blast
wasn't it I'm not sure I don't remember I just remember it was really nice down
there we didn't she said it was being really cold and snowing up there in your
last day that day where's the spring flowers there yep yeah it was green
grass when we were in debt and Heaston last time mm-hmm that was the
same with us look at the greenery mm-hmm I saw a trucker jukeboxes videos today
and he was up in North Carolina the same thing it's all green no they're in the
same 72 degrees that's a really nice area I like North Carolina not a lot
y'all sure do don't get over there enough yeah kind of
been getting shorter trips here the last couple of weeks but hopefully they'll
change how do you maybe noticed a break volume that's of difference going on
with Canada I mean I think we're heading into a recession and yeah
and that you will too if we do yeah for sure that that will definitely happen so
far I haven't really noticed too much like we I've been getting loads every
time I want to go and I get a load right away it just not been super long trips
but it seems like I get a little right away so it might take longer for it I
didn't think about that but for you guys to feel it because as far as Frank
coming into Canada yeah brother plenty of it going to Canada I'm not sure if
there is usually it's the opposite usually there is lots of freight going
to the US but not so much coming back you manufactured goods is that what you
did not at all yeah yeah just just anything that goes in a dry drive van
and I will put you down over there but yeah so that's pretty much what we do is
anything that goes in a drive and is pretty much more evolved I mean we do a
little bit of liquid stuff but for a most most part that's dry goods
all right well we'd better let you guys go y'all
say how to roadie and go over and check out his channel if you would please yeah
definitely you know you might not regret it right
hey this is my cup of tea yeah yeah we we go down a road and we
travel Canada in the United States so you get to sequel to the countries and
and some nice scenery is up in Canada it's for sure also here in the US but
that's like a it both countries that's like I'm gonna ask my pop yeah so you
guys be safe out there I will catch you on the flip side well there goes Chuck
or Rudy everybody
-------------------------------------------
Was sind Faszien? Mit Faszientraining gegen Verspannungen - Duration: 3:54.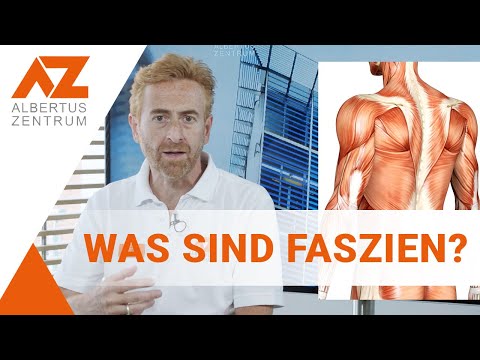
-------------------------------------------
프라이탁은 짝퉁 덕에 유명해졌다? [브랜드 인사이트] Freitag Story (ENG SUB) - Duration: 3:06.
It's made of recycled material but very expensive bag costing an average of 500,000 Won.
Despite of the expensive price, Freitag sells globally 200,000 units every year.
Today, I'm going to introduce Freitag.
Zurich, Switzerland, is a city over 400 meters above sea level.
It rains 127 days a year.
In other words, 1 day out of 3 days has rainy weather.
At that time, two brothers who came to Zurich to be designers.
they always had to worry about their sketches getting wet. Because they rode bikes everyday.
One day in 1993, the brothers saw a noisy truck outside the window of their apartment.
That truck used a tarpaulin to keep out of the rain. It inspired them
and let them to make their own bags after buying the second-hand truck tarpaulin.
This bag is the main model of Freitag, F13 TOP CAT.
And the brother who made this bag was Freitag.
This bag was inspired by bag of paperboy and postman moving by bikes in Zurich.
And the first 40 bags were sold for postman.
Freitag, known as the mailman's messenger bag, gradually became famous.
It moved away from Zurich to other big cities and sold well.
Meanwhile, Freitag met the opportunity to introduce itself throughout the Europe.
Because Migros, a Swiss supermarket chain, had launched the Donnerstag bag, the fake version of Freitag.
Freitag means Friday and Donnerstag means Thursday.
And then, Swiss broadcasting stations reported about Migros' fake brand and criticized it serious.
As the controversy intensified, Migros recalled all of its products.
In this, Freitag became a famous brand in Europe, including Switzerland.
What's interesting is that the awarder was Migros' CEO when Freitag won the prize at the Swiss Awards in 2012.
Marcus Freitag acceptance speech at the awards was very impressive.
"Actually, I stole a bag of Donnerstag from Migros in that time."
"It's the only thing I've ever stolen in my life."
Recently Freitag becomes increasingly popular with eco-friendly and up-cycling trend.
It uses 30 tons of tarpaulin, 150,000 seatbelts, and 18,000 bike tubes a year.
These are all second-hand products and cleansed by rainwater of Zurich.
Recently, It has developed its own fabric called F-ABRIC and sells clothing which can be decomposed 100% by the ground.
I hope the Freitag, the leader in up-cycle, trying to protect the environment will continue to thrive.
Thank you for watching so far. Justin.
-------------------------------------------
【あるある】ぼなーるちゃんねると野球コラボ!みんな共感の珠玉のあるある完全再現!【野球】 - Duration: 4:56.
-------------------------------------------
Emmerdale's real-life couple in on-screen drama as Cain is blamed for Rhona's accident [Soaps] - Duration: 4:00.
Getty ImagesDave J Hogan Emmerdale's real-life couple Jeff Hordley and Zoe Henry will feature in the same storyline tonight (February 21) – well, kind of – as Cain Dingle gets the blame for Rhona Goskirk's horror accident
A dramatic double bill this evening sees Rhona's life hang in the balance after she's caught up in a tractor crash at Butler's Farm
Married couple Jeff and Zoe, who play Cain and Rhona, rarely have any crossover in terms of their plotlines in the ITV soap
However, even though they still don't interact too much in tonight's double bill, the episodes see Cain's name dragged through the mud after a horror incident for Rhona
Thursday's big scenes see Rhona's boyfriend Pete Barton (Anthony Quinlan) get behind the wheel of a tractor at the farm, unaware that it's dodgy
When the brakes fail, he goes crashing into a barn and knocks over Rhona, who's there on vet duties
As Rhona is stretchered into an ambulance and rushed to hospital, Pete bitterly blames Cain for everything – complaining that he should have been pre-warned about the tractor problems
In fact, Cain did tip off his stepson Matty Barton, who failed to pass the message on to Pete
Matty feels terrible that he didn't take enough notice of Cain, having been too caught up in their recent tensions
Will he bring himself to confess that he's the one in the wrong? Emmerdale's Jeff and Zoe tied the knot in 2003 and they have two children together
The show previously gave a nod to this in 2017, when Rhona named Cain as her fantasy one-night stand
Emmerdale airs these scenes tonight at 7pm and 8pm on ITV. Read more news, spoilers and gossip on our Emmerdale homepageDigital Spy Soap Scoop video - hit play below for all the latest Emmerdale spoilers, as Maya prepares to sleep with Jacob, and Kerry searches for details on Amy
Want up-to-the-minute soaps news, spoilers and gossip on your social feeds? Just hit 'Like' on our Digital Spy Soaps Facebook page and 'Follow' on our @soapscoop Twitter account
-------------------------------------------
PARLE-MOI d'ISABELLE BOULAY - Duration: 3:11.
-------------------------------------------
Putin's New Missile Threat Against America - Duration: 2:34.
-------------------------------------------
Beat Karaoke || Beat K LK Cha Cha Trữ Tình Mới Nhất - Hát Cho Người Đang Yêu - Lưu Chí Vỹ ✔ - Duration: 14:00.
-------------------------------------------
로꼬 (Loco) - 엉켜 (Feat. pH-1) Official Music Video (ENG/CHN) - Duration: 4:09.
For the next few days
I'll be on my personal schedule, not going away or anything
Diving into 'Do Not Disturb' mode
settle down on the sofa in the living room
Eat alone no more drink alone no more losing focus temperature rises
Lying entangled feeling the speed of two days zoom by like 2 seconds
Don't you know I'm Loco
Dig inside the sheets because I don't want to wake up
Sorry but I'll be rejecting calls missing calls so no one can find me
Someday again, I'll be on my way (to work)
Until then, I'm nobody
Don't know the color of the window behind the curtains
If there's no schedule, turn off the alarm
No need to stay alone no more
Throw my phone away and with you all night
You and I we're tangled, so we can't detangle like earphones
My body is tangled, seriously want to collapse here
It's been a long time since I had a break
Put into action the plans that have been postponed
Play eat and sleep,there's so much things to do. I need multiple alter egos
Girl I'mma chill with you
I just wanna be with you
Don't want to do anything that requires hard work especially after actively protesting
Just me and you
Yea we gon' be at home
Sleep and snore
I'm like ZZ
Wake me up
Where should we go
Baby please please
Where you goin just stay by my side
It's dangerous outside the blankets Impossible mission
Why ask for trouble just plant right next to me
I just want to stay like this tangled with you
Sorry but I'll be rejecting calls missing calls so no one can find me
Someday again, I'll be on my way (to work)
Until then, I'm nobody
Don't know the color of the window behind the curtains
If there's no schedule, turn off the alarm
No need to stay alone no more
Throw my phone away and with you all night
You and I we're tangled, so we can't detangle like earphones
My body is tangled, seriously want to collapse here
Sorry to everyone, I'm currently absent
Mm right mm right
There's no regrets if a day goes by
Your limbs and my limbs are
Sorry to everyone, I'm currently absent
Mm right mm right
There's no regrets if a day goes by
Your limbs and my limbs are
You and I we're tangled, so we can't detangle like earphones
My body is tangled, seriously want to collapse here
Don't know the color of the window behind the curtains
If there's no schedule, turn off the alarm
No need to stay alone no more
Throw my phone away and with you all night
-------------------------------------------
【MUKBANG】 Crispy & Sticky!! Pork And Grated Yam Rice Bowl [8000kcal] [CC Available] - Duration: 5:23.
Hello it's Kinoshita Yuka (Eng by ~AphexxLegend~)
So today tadaa I've made some crispy torotoro (yam) its made with crispy pork and tororo
I made a bit too much of the tororo grated yam and its covered the pork I made the pork to a crispy perfection
lets see how its made
These are the ingredients pork starch vegetable oil sugar salt mirin sake grated ginger
grated garlic rice mizuna herb yam and yolks
Add starch to pork
Add 3 milimeters of vegetable oil to a pan and once it comes to heat fry the pork
Once it takes on color drain it of oil
In another frying pan add sugar soy sauce mirin sake and grated ginger
once it heats up add the pork we made previously
I can eat bucket loads of this stuff
plate out the rice and our herb
pork
delish
tororo yam
its hiding all the pork
yolk
it broke
Are the yolks are on tadaa its all done
It looks delicious I have a japanese style soup with leek and minced beef
itadakimasu
The pork looks amazing lets eat it with the yam
bust up some yolks
its def gonna be yummy
the surface of the pork is so crispy its so very fatty and delish
its topped with all this tororo making it so yummy
this mustard green is so yummy and crunchy
there are so many different types of mouthfeels in this dish the gooey tororo and crisp pork and crunchy mustard green
The pork is so sweet and salty
The leek is so tender and sweet
I really love that fatty pork
lets take a moment to add some wasabi and soy sauce
this stuff goes awesome with tororo
I love mixing light and fresh flavors with heavy rich foods
(RAW EGGS ARE SAFE IN JAPAN salmonella = no smelly = no safe = yes tasty =yes)
Since I covered it in so much starch it stays crispy for so long
last mouthful itadakimasu
gochisosamadeshita the crispy gooey bowl was so yummy
its a perfect balance of fresh and rich flavors
whenever you add deep fried things it really makes things better deep fried stuff is the G.O.A.T.
It was all so yummy want you all please give it a try And as always thank you for watching if there's anything you want
Me to do or eat comment section if you like this video plz hit the like and subscribe buttons BAI BAI
lets all eat yummy stuff tomorrow
-------------------------------------------
Sexy modelka venku bez podprsenky: Zima jí poškádlila bradavky! - Duration: 1:18.
Zahalila se do černé od hlavy až k patě, přesto byla sexy. Postaraly se o to její vystouplé bradavky, které byly pod rolákem dost viditelné
Pro modelku je však taková provokace tou nejmenší. Ráda totiž své prsa vystavuje i nahá
Na společenské akce chodí Joy Corrigan zásadně v šatech s hlubokým výstřihem, nebo si rovnou vezme takové, které jí bradavky vůbec nezakryjí
A když na to přijde, nemá problém se svléknout úplně a zapózovat před objektivem jen v plavkových kalhotkách
Stud je jí zkrátka cizí.
-------------------------------------------
K.D《不染》【不願染是與非,怎料事與願違...】K.D Music ♫ - Duration: 5:32.
-------------------------------------------
Sing at Noraebang - the Korean karaoke - Duration: 0:34.
Try the Korean version of karaoke called Noraebang
Sing your heart out with your new friends
Take a shot at your favorite K-pop songs
Or search the archive for some 90s classics
It's all about having fun!
-------------------------------------------
US : Zion Williamson blows apart sneaker, heads to locker room with game-ending knee injury - Duration: 2:22.
-------------------------------------------
'컬투쇼' 이필모 "결혼, 꿈 같지는 않아..첫날부터 현실" - Duration: 2:08.
-------------------------------------------
'슬플 때 사랑한다' 박한별↔박하나, 2인 1역 '파격멜로'(ft.집착 류수영)[종합] - KN Channel - Duration: 6:29.
-------------------------------------------
美빌보드 "블랙핑크 북미 투어, 미국 내 인기상승 명확한 징후" - Duration: 3:39.
미국 유력 음악 체 빌보드가 걸그 블랙핑크의 행보 긍정적으로 내다 다. 빌보드는 0일(현지시각) 블랙핑크는 어떻게 단 한 번의 미국 공연 없이 북미 레나 투어를 성사 켰나(How BL CKPINK Bo ked a Nor h America Arena To r Before laying a ingle U.S Show)'라는 제목으로 블랙핑크 집중 조명했다. 빌보드는 "블 핑크가 4월 12 과 19일 코첼라 공연과 함께 4월 17일 LA를 시 으로 3주간 북미 투어 공연 계획 확정 지었다"면 "북미 공연 경 이 없음에도 불구 고 미주 여러 도 의 공연 계획을 표하며 미국 내 기 상승의 징후를 보여주고 있는 그 이다"고 극찬했다 또한 블랙핑 가 1570만 명 인스타그램 팔로 , 1920만 명 유튜브 채널 구 자 수를 보유하고 있다는 것을 언급 며 "블랙핑크는 국 무대에 오를 있을 만한 글로 소셜 네트워크를 이미 소유하고 있 "고 설명했다. 미국 최대 음악 페스티벌 '코첼라 와 이번 블랙핑크 북미 투어를 주최 는 공연기획사 골 보이스는 "블랙핑 의 첫 등장부터 목해왔다"면서 " 미 경험이 부족함 도 불구하고 이러 무궁무진한 발전 가능성이 블랙핑크 공연 주최를 주저 지 않았던 이유" 고 밝혔다. 블 핑크는 최근 미국 유명 프로그램인 BS '레이트쇼' ABC '굿모닝 아메리카'에 이어 ABC '스트라한 앤드 사라'까지 요 방송에 출연하 글로벌 걸그룹의 위상을 과시했다. 블랙핑크는 K팝 초로 오는 4월 2일. 19일, 국 최대 음악축제 '코첼라 밸리 직 앤드 아츠 페 티벌' 무대에도 른다. 이어 월 17일 로스앤 레스를 시작으로 월 24일 시카고 4월 27일 해 턴, 5월 1일 어크, 5월 5일 애틀랜타, 5월 일 포트워스 등 6개 도시 6회 공연으로 북미 투 에 나선다. Y N Star 지승 기자 (jiwi @ytnplus. o.kr) [사 제공 = YG엔터 인먼트]
No comments:
Post a Comment